TTEC Tischkühlturm, computergesteuert (PC)
INNOVATIVE SYSTEME
The Computer Controlled Bench Top Cooling Tower, "TTEC", has been perfectly designed to offer the students the opportunity of exploring the design, construction and operating characteristics of a modern water evaporation cooling system.
Erweiterungen
Laboratorien
ÄHNLICHE NEUIGKEITEN
ALLGEMEINE BESCHREIBUNG
The Computer Controlled Bench Top Cooling Tower, "TTEC", includes a pump that impels hot water from a tank (with level switch and heating element) to the manifolds located at the top of the cooling tower. Water flow can be adjusted by a manual needle valve.
A temperature sensor located at the top of the unit measures the temperature of the water just before entering the tower. Water cools down as it falls through the manifolds of the tower, and finally falls into the tank where its temperature is measured again.
A fan propels atmospheric air with an accurate control of the air flow introduced in the tower. The air passes through wet bulb and dry bulb sensors before entering the column.
As air flows through the column, its temperature and humidity rise. On the other hand, water temperature falls. At the upper side there are other two dry bulb and wet bulb temperature sensors.
This Computer Controlled Unit is supplied with the EDIBON Computer Control System (SCADA), and includes: The unit itself + a Control Interface Box + a Data Acquisition Board + Computer Control, Data Acquisition and Data Management Software Packages, for controlling the process and all parameters involved in the process.
ÜBUNGEN UND GEFÜHRTE PRAKTIKEN
GEFÜHRTE PRAKTISCHE ÜBUNGEN IM HANDBUCH ENTHALTEN
- Process observation inside a bench top cooling tower.
- Determination of evaporation velocity.
- Mass balance. Use of psychrometric charts.
- Energy balance.
- Effect of cooling load against Wet bulb approach.
- Relation between air velocity, wet bulb approach and head loss.
- Determination of the cooling capacity.
- Determination of the cooling capacity for different cooling towers.
- Thermodynamic properties.
- Evaporation from a wet bed.
- Observation of water flow pattern and distribution.
- Control system: Temperature sensors calibration.
- Control system: PID temperature control.
- Control system: Flow sensors calibration.
- Study of flow sensor hysteresis.
- Control system: Determination of adjustment parameters of a PWM controller.
- Differential pressure sensors calibration.
MEHR PRAKTISCHE ÜBUNGEN FÜR DAS GERÄT
- Variation of specific enthalpy with pressure.
- Properties of air.
- Use of a psychometric map.
- Determination of water flow.
- Many students view results simultaneously. To view all results in real time in the classroom by means of a projector or an electronic whiteboard.
- Open Control, Multicontrol and Real Time Control. This unit allows intrinsically and/or extrinsically to change the span, gains, proportional, integral, derivative parameters, etc, in real time.
- The Computer Control System with SCADA and PID Control allow a real industrial simulation.
- This unit is totally safe as uses mechanical, electrical and electronic, and software safety devices.
- This unit can be used for doing applied research.
- This unit can be used for giving training courses to Industries even to other Technical Education Institutions.
- Control of the TTEC unit process through the control interface box without the computer.
- Visualization of all the sensors values used in the TTEC unit process.
- By using PLC-PI additional 19 more exercises can be done.
- Several other exercises can be done and designed by the user.
ÄHNLICHE VERFÜGBARE GERÄTE
ERGÄNZENDE AUSRÜSTUNG
Tisch-Kühlturm
Tablettentrockner, computergesteuert (PC)
Sprühtrockner, computergesteuert (PC)
Sprühtrockner
Gerät für Sprühtrocknung und -kühlung, computergesteuert (PC)
Gefriertrockner
QUALITÄT
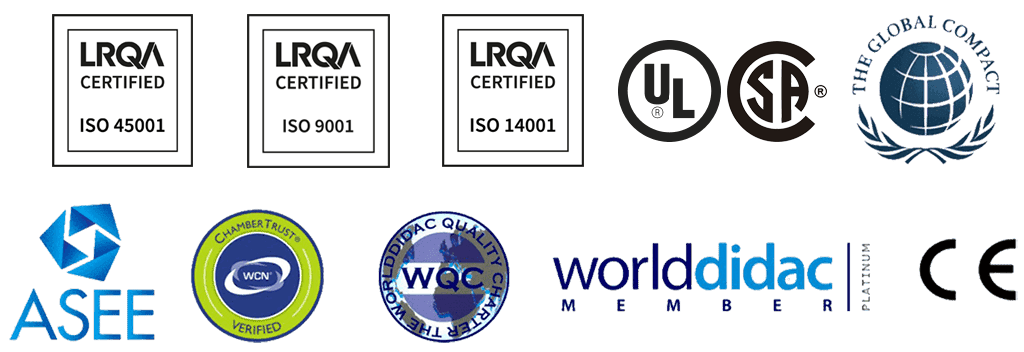
KUNDENDIENST
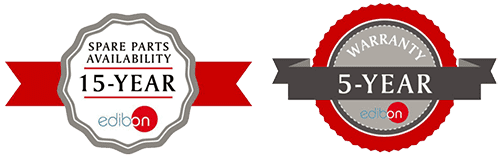