What are DFIGs?
Wind Energy and its technological evolution
Wind energy is the kinetic energy that is obtained from the wind and is used to convert it into mechanical energy through wind turbines. From mechanical energy, it is transformed into electrical energy or other forms useful for human activity.
In recent years, wind energy has grown almost exponentially compared to the rest of conventional energy. The key to all this has been the amazing technological evolution that has led us to the current situation. Power electronics, control logic, the advance in fluid mechanics, the improvement of software tools for the study of mechanical loads in wind turbines and the creation of mathematical models, has led to a great evolution in the development of wind turbines and therefore, wind farms.
At the head of these large wind turbines are those with a very particular and refined technology, the Double-Powered Electric Generators (doubly-fed) or also known as DFIG, capable of generating electrical energy within a wide range of wind speeds.
What are DFIGs?
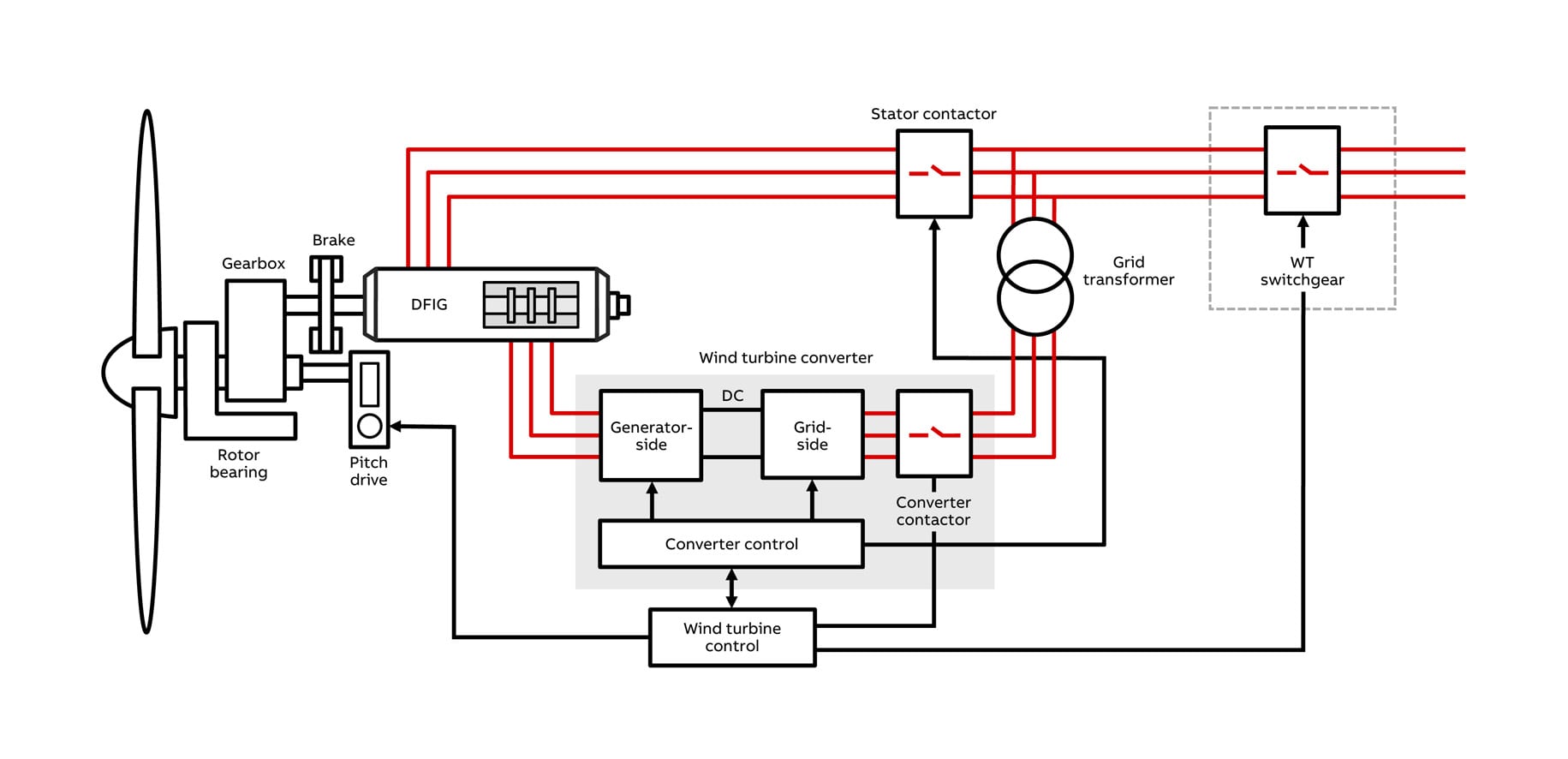
Double-Fed Electric Generators (DFIG) are asynchronous induction machines from which electrical energy can be extracted from both the stator winding and the rotor winding thanks to state-of-the-art technology based on bi-directional inverters (back to back inverters). These inverters are able to control the power flow bidirectionally between the machine rotor and the power grid.
DFIG generators are relatively complex machines. They consist of a wound rotor with three slip rings and a stator with its own windings. The stator is connected directly to the network and provides part of the nominal power of the machine. The bi-directional inverter (back to back invert) is connected to the rotor through the slip rings. Here the power electronics play a fundamental role since, with the correct modulation of the IGBTs, we will be able to extract electric power from the rotor even at low wind speeds.
What technology do DFIG wind generators use?
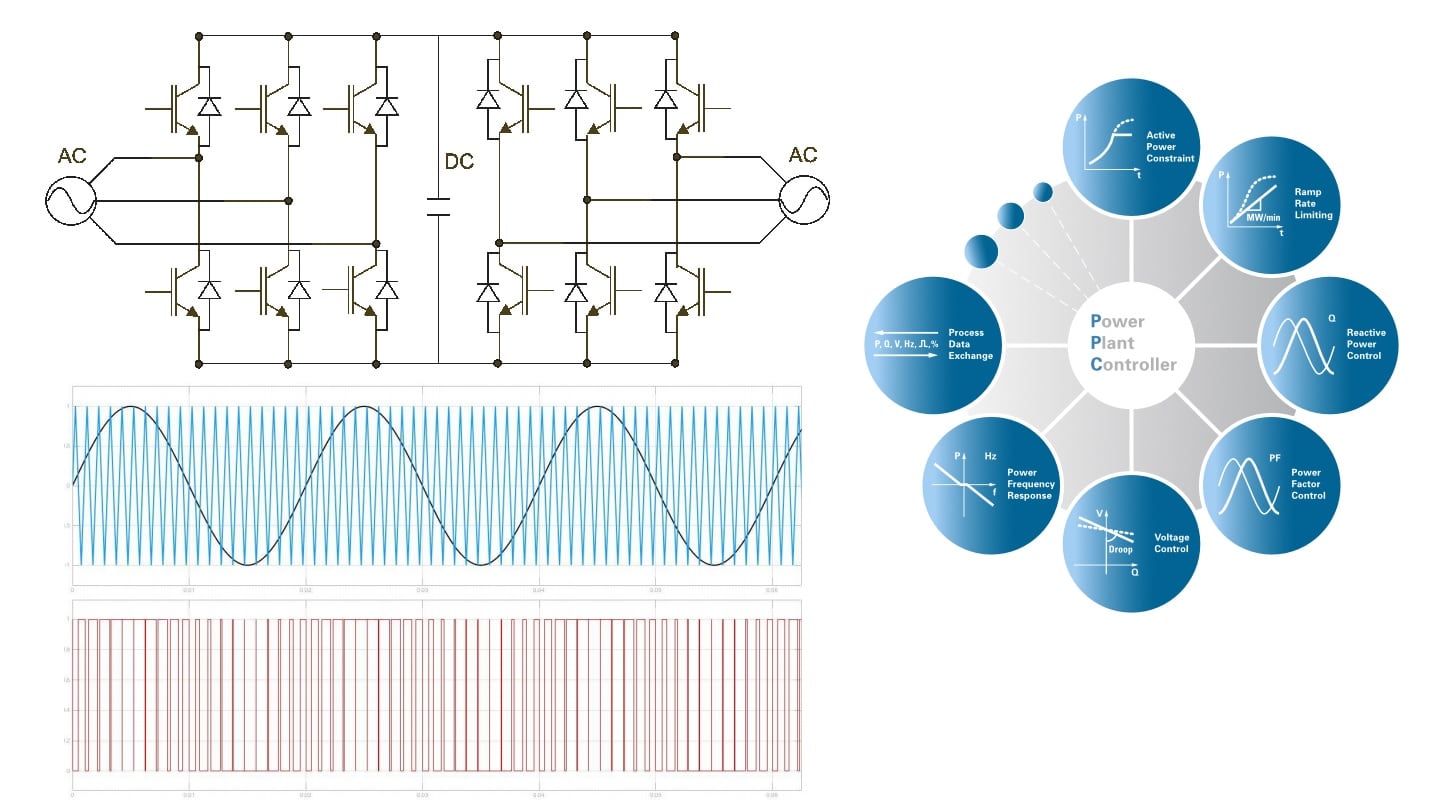
Thanks to the bi-directional inverters (back to back inverters) and the use of double-fed generators, today it is possible to provide greater robustness and reliability to the national electricity grid in the presence of faults. This power in wind generators and parks is known as Fault Ride Through (FRT), and is the ability of wind turbines to remain connected to the grid in the presence of electrical failures causing the voltage drop in the grid. The IEC 61400-21 standard is very strict in this area, which requires a series of maneuvers in wind farms in the presence of an electrical fault without being able to disconnect from the grid until after a few seconds.
Edibon at the forefront of wind technology DFIG
There is no impossible challenge for us, and that is why in recent years we have developed a unit to study the dynamics of wind turbines and doubly-fed electric generators (DFIG). To achieve this challenge, electrical, electronic and software engineers have developed a scale hardware model and a data control and acquisition system that simulates the mechanical conditions of the turbine and the DFIG generator. Some variables that are monitored for turbine control are torque, wind and rotor speed of the machine and pitch angle. The mechanical part of the turbine is simulated by means of a high-precision servo motor coupled to a three-phase doubly-fed induction generator exactly the same as real DFIGs.