At EDIBON, we are committed to strengthening skills as a strategic pillar for the competitiveness and social well-being of the European Union. Proper training not only boosts the economy but also enables individuals to fully participate in society and democracy.
AE-PLC-FMS5 Flexible Manufacturing System for Transport, Classification, Selection, and Pneumatic Handling
INNOVATIVE SYSTEMS
The Flexible Manufacturing System for Transport, Classification, Selection, and Pneumatic Handling, "AE-PLC-FMS5," designed by EDIBON, enables the study and practice of an automated production cycle consisting of 9 distinct workstations. This system integrates all the mentioned workstations, along with a parts distribution station, an identification station, a storage station, a robotic arm, and a multi-part feeding station to ensure the comprehensive operation of the system.
RELATED NEWS
General Description
Flexible Manufacturing System for Transport, Classification, Selection, and Pneumatic Handling, "AE-PLC-FMS5," is a highly adaptable and configurable system designed for the study and application of advanced automation principles within the context of Industry 4.0 and Industry 5.0. This equipment integrates key technologies such as automated control, inter-device networking through smart networks, PLC programming of assembly lines, and real-time data analysis, allowing users to explore the capabilities of digitized and connected manufacturing that characterize the Fourth Industrial Revolution and pave the way for the Fifth Industrial Revolution.
It consists of nine interconnected stations that perform specific tasks of distribution, identification, classification, transport, pneumatic handling, automated processing (drilling and polishing study), robotic arm assembly, and vertical storage of parts. Each of these workstations requires its own PLC from the selected brand (PANASONIC, SIEMENS, ALLEN BRADLEY, MITSUBISHI and/or OMRON), allowing users to explore how advanced control and production concepts are applied in an automated manufacturing line. The workflow is coordinated by a central PLC system (from the same brand chosen for the stations) and an Ethernet network, making the "AE-PLC-FMS5" a comprehensive learning resource for those interested in automation engineering and flexible manufacturing.
The included workstations are:
- Parts Distribution Workstation, "AE-PLC-DS": Provides parts of different colors, materials, and heights to the Identification Workstation, "AE-PLC-SIP".
- Classification Workstation, "AE-PLC-CF": Selects parts that meet the required patterns for color, material, and height, while discarding the rest.
- Linear Transport Workstation, "AE-PLC-T": The selected parts are added to this workstation, where valid pieces are positioned and transported to the next workstation.
- First Pneumatic Handling Workstation, "AE-PLC-MAN": One of the pneumatic manipulators takes parts from the Linear Transport Workstation, "AE-PLC-T", and places them in the Rotary Table Workstation: Automated Processing Control (drilling and polishing study), "AE-PLC-MR3" to assemble an auxiliary part within the base piece. The pneumatic manipulator then returns the parts to the linear transport system to continue the process.
- Robotic Arm Workstation, "AE-BR": The robotic arm picks various parts from the Multiple Parts Feeding Workstation, "AE-PLCMA", and assembles them into the base piece located on the Linear Transport Workstation, "AE-PLC-T".
- Vertical Storage Workstation, "AE-PLC-ALV": Completed parts are temporarily stored in this system until required by the operator. The system includes a vertical storage unit and a three-dimensional XYZ manipulator that retrieves parts from the linear transport system and places them in the desired storage position. When a part is needed, the XYZ manipulator picks it up and returns it to the linear transport system.
- Second Pneumatic Handling Workstation, "AE-PLC-MAN": This workstation picks parts from the Linear Transport Workstation, "AE-PLC-T", and places them in the Classification Workstation, "AE-PLC-CF". This workstation separates parts based on the specifications configured by the operator.
The system allows students and instructors to delve into fundamental concepts of industrial automation. Through its use, students acquire practical skills in designing and operating automated systems, gaining a deep understanding of the coordinated work across the various workstations of a real production line. This configurable system has been carefully designed so that each of its workstations performs specific functions that simulate real industrial processes.
The recommended Automation System Simulation Software, "AE-AS," enables the simulation of industrial processes in both 2D and 3D, providing full control and supervision, allowing users to safely experiment with automation software in a protected environment.
Exercises and guided practices
GUIDED PRACTICAL EXERCISES INCLUDED IN THE MANUAL
Practical possibilities to be done with the Flexible Manufacturing System for Transport, Classification, Selection, and Pneumatic Handling (AE-PLC-FMS5):
- Introduction to flexible manufacturing system (FMS).
- Introduction to pneumatics and electro-pneumatics.
- Introduction to vacuum technology.
- Study of the sensor detection.
- Testing the digital inputs and outputs of the automatic system through a PLC.
- Modify manufacturing parameters through the PLC.
- Configuration of a pneumatic application.
- Introduction to the Human-machine interface systems (HMI).
- Study of an automatic control of an industrial system.
- Control of the flexible manufacturing system through a central PLC in an Ethernet network with local PLC in each workstation.
- Manage the flexible manufacturing system through the HMI device.
Practical possibilities to be done with the workstation alone: - Parts Distribution Workstation (AE-PLC-DS).
- Manual control of a Feeding system.
- Automatic control of a Feeding system.
- Change the parameters of the Feeding process.
- Optimize the process time.
- Study and analysis of the faults inserted in the process with the fault generation module.
- Parts Identification Workstation (AE-PLC-SIP).
- Manual control of a quality control system.
- Automatic control of a quality control system.
- Change the parameters of the quality control system.
- Optimize the process time.
- Study and analysis of the faults inserted in the process with the fault generation module.
- Sorting Workstation (AE-PLC-CF).
- Manual control of a sorting system.
- Automatic control of a sorting system.
- Change the parameters of the sorting process.
- Optimize the process time.
- Study and analysis of the faults inserted in the process with the fault generation module.
- Linear Transport Workstation (AE-PLC-T).
- Manual control of a transporting system.
- Automatic control of a transporting system.
- Change the parameters of a transporting process.
- Optimize the process time.
- Study and analysis of the faults inserted in the process with the fault generation module.
- Pneumatic Handling Workstation (AE-PLC-MAN).
- Manual control of a handling system.
- Automatic control of a handling system.
- Automatic control of a handling and sorting system.
- Change the parameters of the process.
- Optimize the process time.
- Study and analysis of the faults inserted in the process with the fault generation module.
- Rotary Table Workstation: Automated Processing Control (drilling and polishing study) (AE-PLC-MR3).
- Manual control of the rotary table system.
- Manual control of the quality control and drilling process on a rotary table.
- Automatic control of the rotary table system.
- Automatic control of the quality control and drilling process on a rotary table.
- Change the parameters of the rotary table process.
- Optimize the process time.
- Study and analysis of the faults inserted in the process with the fault generation module.
- Robotic Arm Workstation (AE-BR).
- Introduction to robotic systems.
- Robotic arm configuration.
- Set a simple movement of the robotic arm.
- Introduction to pneumatics and electro-pneumatics.
- Configuration of a pneumatic application.
- Set a simple pick and place function with the robotic arm.
- Multi-Part Feeding Workstation (AE-PLC-MA).
- Configuration of the robotic arm as a pick and place system.
- Change the parameters of the pick and place process.
- Optimize the pick and place process.
- Configuration of the robotic arm as a mounting system.
- Change the parameters of the mounting process.
- Optimize the mounting process.
- Vertical Storage Workstation (AE-PLC-ALV).
- Introduction to the flexible manufacturing system: Identification of unit components.
- Introduction to pneumatics and electro-pneumatics: Identification of components.
- Configuration of a pneumatic application.
- Operation of pneumatic system: Introduction to pneumatic actuators.
- Study of sensor detection.
- Manual control of gantry system.
- Automatic control of gantry system.
- Industrial application example.
- Industrial application tuning.
- Fault inserted analysis and diagnosis.
- Flexible Manufacturing System (FMS).
Practical possibilities to be done with the optional software Automation Systems Simulation Software (AE-AS):
- Introduction to the SCADA control system.
- OPC server system with Ethernet.
- SCADA control of an automatic industrial system through PC.
MORE PRACTICAL EXERCISES TO BE DONE WITH THE UNIT
- Many students view results simultaneously. To view all results in real time in the classroom by means of a projector or an electronic whiteboard.
- Open Control, Multicontrol and Real Time Control. This unit allows intrinsically and/or extrinsically to change the span, gains, proportional, integral, derivative parameters, etc, in real time.
- The Computer Control System with SCADA and PID Control allow a real industrial simulation.
- This unit is totally safe as uses mechanical, electrical and electronic, and software safety devices.
- This unit can be used for doing applied research.
- This unit can be used for giving training courses to Industries even to other Technical Education Institutions.
- Control of the AE-PLC-FMS5 unit process through the control interface box without the computer.
- Visualization of all the sensors values used in the AE-PLC-FMS5 unit process.
- Several other exercises can be done and designed by the user.
SIMILAR UNITS AVAILABLE
6.2.6.- FLEXIBLE MANUFACTURING SYSTEMS WITH PLC
AE-PLC-FMS2
The Flexible Manufacturing System for Transport, Assembly, Selection, Screwing, and Storage, "AE-PLC-FMS2", is a highly adaptable and configurable system designed for the study and application of advanced automation principles within the context...
6.2.6.- FLEXIBLE MANUFACTURING SYSTEMS WITH PLC
AE-PLC-FMS3
Flexible Manufacturing System for Transport, Assembly, Selection (Material and Color), and Storage
The Flexible Manufacturing System for Transport, Assembly, Selection (Material and Color), and Storage, "AE-PLC-FMS3", is a highly adaptable and configurable system designed for the study and application of advanced automation principles within...
6.2.6.- FLEXIBLE MANUFACTURING SYSTEMS WITH PLC
AE-PLC-FMS4
Flexible Manufacturing System for Filtering, Mixing, Industrial Process Control, and Bottling
The Flexible Manufacturing System for Filtering, Mixing, Industrial Process Control, and Bottling, "AE-PLC-FMS4", is a highly adaptable and configurable system designed for the study and application of advanced automation principles within the...
6.2.6.- FLEXIBLE MANUFACTURING SYSTEMS WITH PLC
AE-PLC-FMS6
Flexible Manufacturing System for Feeding and Classification
The Flexible Manufacturing System for Feeding and Classification, "AE-PLC-FMS6", is a highly adaptable and configurable system designed for the study and application of advanced automation principles within the context of Industry 4.0 and Industry...
6.2.6.- FLEXIBLE MANUFACTURING SYSTEMS WITH PLC
AE-PLC-FMS7
Flexible Manufacturing System for Feeding, Identification, Classification, and Transport
The Flexible Manufacturing System for Feeding, Identification, Classification, and Transport, "AE-PLC-FMS7", is a highly adaptable and configurable system designed for the study and application of advanced automation principles within the context...
6.2.6.- FLEXIBLE MANUFACTURING SYSTEMS WITH PLC
AE-PLC-FMS1
Flexible Manufacturing System for Transport, Assembly, Pressing, Selection, Screwing, and Storage
The Flexible Manufacturing System for Transport, Assembly, Pressing, Selection, Screwing, and Storage, "AE-PLC-FMS1", is a highly adaptable and configurable system designed for the study and application of advanced automation principles within the...
6.2.6.- FLEXIBLE MANUFACTURING SYSTEMS WITH PLC
AE-PLC-FMS14
Flexible Manufacturing System for Industrial Process Control, Filling, Sealing, and Storage
The Flexible Manufacturing System for Industrial Process Control, Filling, Sealing, and Storage, "AE-PLC-FMS14", is a highly adaptable and configurable system designed for the study and application of advanced automation principles within the...
6.2.6.- FLEXIBLE MANUFACTURING SYSTEMS WITH PLC
AE-PLC-FMS15
Flexible Manufacturing System for Feeding, Assembly, Robotic Handling, and Transport
The Flexible Manufacturing System for Feeding, Assembly, Robotic Handling, and Transport, "AE-PLC-FMS15", is a highly adaptable and configurable system designed for the study and application of advanced automation principles within the context of...
SUPPLEMENTARY EQUIPMENT
6.2.6.- FLEXIBLE MANUFACTURING SYSTEMS WITH PLC
AE-PLC-FMS1
Flexible Manufacturing System for Transport, Assembly, Pressing, Selection, Screwing, and Storage
The Flexible Manufacturing System for Transport, Assembly, Pressing, Selection, Screwing, and Storage, "AE-PLC-FMS1", is a highly adaptable and configurable system designed for the study and application of advanced automation principles within the...
6.2.6.- FLEXIBLE MANUFACTURING SYSTEMS WITH PLC
AE-PLC-FMS2
Flexible Manufacturing System for Transport, Assembly, Selection, Screwing, and Storage
The Flexible Manufacturing System for Transport, Assembly, Selection, Screwing, and Storage, "AE-PLC-FMS2", is a highly adaptable and configurable system designed for the study and application of advanced automation principles within the context...
6.2.6.- FLEXIBLE MANUFACTURING SYSTEMS WITH PLC
AE-PLC-FMS3
Flexible Manufacturing System for Transport, Assembly, Selection (Material and Color), and Storage
The Flexible Manufacturing System for Transport, Assembly, Selection (Material and Color), and Storage, "AE-PLC-FMS3", is a highly adaptable and configurable system designed for the study and application of advanced automation principles within...
6.2.6.- FLEXIBLE MANUFACTURING SYSTEMS WITH PLC
AE-PLC-FMS4
Flexible Manufacturing System for Filtering, Mixing, Industrial Process Control, and Bottling
The Flexible Manufacturing System for Filtering, Mixing, Industrial Process Control, and Bottling, "AE-PLC-FMS4", is a highly adaptable and configurable system designed for the study and application of advanced automation principles within the...
6.2.6.- FLEXIBLE MANUFACTURING SYSTEMS WITH PLC
AE-PLC-FMS6
Flexible Manufacturing System for Feeding and Classification
The Flexible Manufacturing System for Feeding and Classification, "AE-PLC-FMS6", is a highly adaptable and configurable system designed for the study and application of advanced automation principles within the context of Industry 4.0 and Industry...
6.2.6.- FLEXIBLE MANUFACTURING SYSTEMS WITH PLC
AE-PLC-FMS7
Flexible Manufacturing System for Feeding, Identification, Classification, and Transport
The Flexible Manufacturing System for Feeding, Identification, Classification, and Transport, "AE-PLC-FMS7", is a highly adaptable and configurable system designed for the study and application of advanced automation principles within the context...
6.2.6.- FLEXIBLE MANUFACTURING SYSTEMS WITH PLC
AE-PLC-FMS14
Flexible Manufacturing System for Industrial Process Control, Filling, Sealing, and Storage
The Flexible Manufacturing System for Industrial Process Control, Filling, Sealing, and Storage, "AE-PLC-FMS14", is a highly adaptable and configurable system designed for the study and application of advanced automation principles within the...
6.2.6.- FLEXIBLE MANUFACTURING SYSTEMS WITH PLC
AE-PLC-FMS15
Flexible Manufacturing System for Feeding, Assembly, Robotic Handling, and Transport
The Flexible Manufacturing System for Feeding, Assembly, Robotic Handling, and Transport, "AE-PLC-FMS15", is a highly adaptable and configurable system designed for the study and application of advanced automation principles within the context of...
Quality
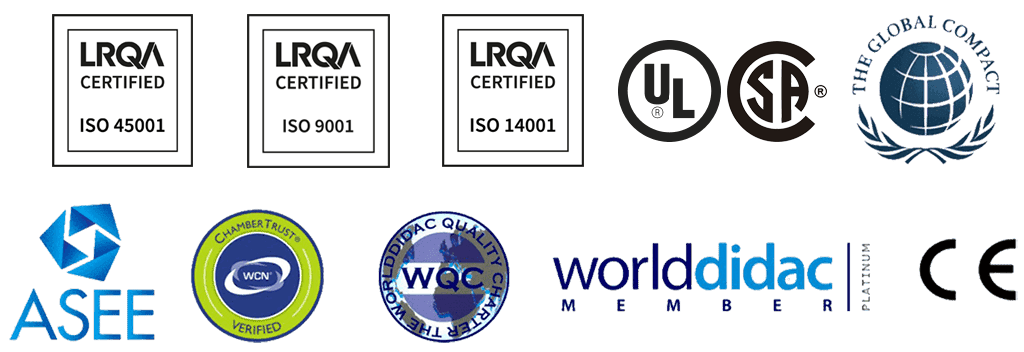
AFTER-SALES SERVICE
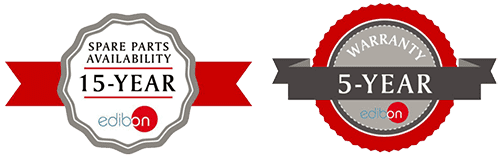