At EDIBON, we are committed to strengthening skills as a strategic pillar for the competitiveness and social well-being of the European Union. Proper training not only boosts the economy but also enables individuals to fully participate in society and democracy.
AE-PLC-MR3 Rotary Table Station: Automated Processing Control (drilling and polishing study)
INNOVATIVE SYSTEMS
The "AE-PLC-MR3" is a processing workstation with a rotary table commanded by a PLC.
RELATED NEWS
General Description
The "AE-PLC-MR3" is a processing workstation with a rotary table commanded by a PLC. This unit takes a piece from the input area, checks if the position of piece is correct, and simulates drilling the piece with a movable drilling machine. Finally the workstation places the piece to the exit piece area. The "AE-PLC-MR3" also includes a polish tool to change the process and simulates the polishing of the piece.
The "AE-PLC-MR3" workstation is designed as a modular system to facilitate the understanding of the unit. The main components are:
- The PLC: is composed by the CPU PLC unit and all the extra modules needed to perform a correct working of the workstation.
- The control panel: with start/stop button, emergency pushbutton, reset button, light indicators to show current state of the process, etc.
- The workstation: is composed by real industrial components used by the industrial processing systems with rotary tables such as limit switch sensors, capacitive sensors, drilling machine, etc.
The "AE-PLC-MR3" is an independent workstation that can work alone and/or in conjunction with other workstations to make up a complete Flexible Manufacturing system*.
*The Flexible manufacturing systems product list is available at "Flexible Manufacturing Systems (FMS)" area of the general catalogue.
Exercises and guided practices
GUIDED PRACTICAL EXERCISES INCLUDED IN THE MANUAL
- Introduction to flexible manufacturing system (FMS).
- Introduction to electrical actuators.
- Study of the sensor detection.
- Manual control of the rotary table system.
- Manual control of the quality control and drilling process on a rotary table.
- Automatic control of the rotary table system.
- Automatic control of the quality control and drilling process on a rotary table.
- Change the parameters of the rotary table process.
- Optimize the process time.
- Study and analysis of the faults inserted in the process with the fault generation module.
SIMILAR UNITS AVAILABLE
6.2.5.3.- ROTARY TABLE WORKSTATIONS
AE-PLC-MR1
The Rotary Table Station: Feeding, Quality Control and Assembly (dimensional study), "AE-PLC-MR1", has been designed by EDIBON to study automatic rotary table systems for mounting, quality control, and feeding parts. It integrates a modular design...
6.2.5.3.- ROTARY TABLE WORKSTATIONS
AE-PLC-MR2
Rotary Table Station: Feeding, Quality Control, and Assembly (material and color study)
The "AE-PLC-MR2" an automatic rotary table with a feeder, quality control and mounting system integrated in it. The "AE-PLC-MR2" has a vertical storage, the system provide pieces one by one to the rotary table, then, a quality control system check...
6.2.5.3.- ROTARY TABLE WORKSTATIONS
AE-PLC-MR4
Rotary Table Station: Filling, Bottling and Capping
The "AE-PLC-MR4" is a rotary table workstation commanded by a PLC that perform the bottling, filling and capping functions.The "AE-PLC-MR4" workstation has been designed as a modular system to facilitate the understanding of the equipment...
SUPPLEMENTARY EQUIPMENT
6.2.5.3.- ROTARY TABLE WORKSTATIONS
AE-PLC-MR1
Rotary Table Station: Feeding, Quality Control and Assembly (dimensional study)
The Rotary Table Station: Feeding, Quality Control and Assembly (dimensional study), "AE-PLC-MR1", has been designed by EDIBON to study automatic rotary table systems for mounting, quality control, and feeding parts. It integrates a modular design...
6.2.5.3.- ROTARY TABLE WORKSTATIONS
AE-PLC-MR2
Rotary Table Station: Feeding, Quality Control, and Assembly (material and color study)
The "AE-PLC-MR2" an automatic rotary table with a feeder, quality control and mounting system integrated in it. The "AE-PLC-MR2" has a vertical storage, the system provide pieces one by one to the rotary table, then, a quality control system check...
6.2.5.3.- ROTARY TABLE WORKSTATIONS
AE-PLC-MR4
Rotary Table Station: Filling, Bottling and Capping
The "AE-PLC-MR4" is a rotary table workstation commanded by a PLC that perform the bottling, filling and capping functions.The "AE-PLC-MR4" workstation has been designed as a modular system to facilitate the understanding of the equipment...
Quality
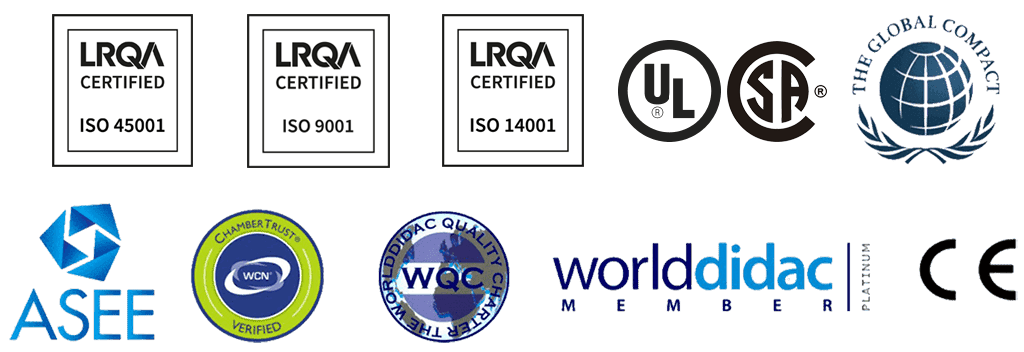
AFTER-SALES SERVICE
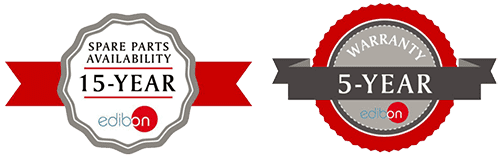