QEDC Unité d´Extraction de Dissolvant en Discontinu, Contrôlée par Ordinateur (PC)
SYSTEMES INNOVANTS
The Computer Controlled Batch Solvent Extraction and Desolventising Unit, "QEDC", is a batch process unit able to perform different solid/liquid extractions.
Expansions
Laboratories
NOUVELLES LIÉES
Description Générale
The Computer Controlled Batch Solvent Extraction and Desolventising Unit, "QEDC", is a batch process unit able to perform different solid/liquid extractions. It is especially suitable for extracting oil from oily seeds and to remove the solvent both from the extracted solids and mixtures. Furthermore, several factors that influence the extraction process can be studied with this unit.
The cylindrical extractor/desolventiser tank with a hinged lid for charging the extraction material has a base slightly inclined towards a port to discharge the extracted and desolventised meal. Material is supported above the base by a perforated plate covered with a fine woven mesh, so solvent may drain through to the miscella tank whilst retaining the solids.
The tank base is equipped with an indirect steam chest for process heating. Direct steam is injected through a distribution pipe positioned above the mesh. A similar distribution pipe positioned near the top of the tank allows solvent to be sprayed uniformly onto the bed of material. This tank is equipped with a sight glass so that the processes can be observed and monitored.
The miscella tank, positioned directly below the extractor to collect the draining liquid, is also a cylindrical vessel incorporating a steam chest as its base and has a base slightly inclined towards a port for discharging the extracted and the dissolvent.
This tank also incorporates a direct steam distribution pipe through which steam can be sprayed uniformly onto the bed of material. This tank is equipped with a suitable level viewer.
The extractor/desolventiser tank and the miscella tank incorporate two safety valves to limit the working pressure to 0.9 bar in order to prevent the vapour condenser inlet pressure exceeding the working pressure in that condenser at the vapour side.
Vapour from the tanks, produced in the desolventising process, is directed by ducting to the solvent condenser and inclined cylindrical glass tube containing a double coil, through which cooling water is circulated. The covers of this condenser are made of stainless steel. The condenser water inlet is controlled by a pressure regulator so that the operating pressure range is not exceed. Thus, the glass coil is prevented from breaking.
Condensate (usually a mixture of solvent and water) drains into the solvent water tank which allows thorough separation of the solvent and water by a gravity process. Note: Only hexane or solvents having a similar specific gravity can be effectively separated in this tank.
Solvent reclaimed from this tank can then be recirculated by the solvent pump at a regulated rate. Excess water overflows to a waste water tank from where it can be disposed of on completion of the process.
Operation at reduced system pressures are achieved by a PTFE double diaphragm type vacuum pump. The outlet of this pump is piped through a flame arrester to a suitable ventilation point.
Each tank is equipped with suitable level viewer or sight glasses so that the processes can be observed and monitored. Pressure and temperature sensors are supplied where necessary, as are adequate sampling and drain valves.
Hexane is the most widely used solvent in the extraction processes and due to the inflammable nature of this product electrical equipment has been kept to a minimum.
Modes of operation:
- Extraction by washing with clean solvent: This involves priming the solvent/water separator tank with solvent and pumping the solvent to the extractor where it percolates through the material bed and drains as miscella in the tank for recirculation.
- Extraction by recirculating miscella: As miscella is formed, steam admitted to the miscella tank causes solvent to evaporate. The vapour is condensed in the solvent condenser and returns to the separator tank from which it is pumped back to the extractor tank.
- Desolventising extracted material: When the extraction is complete, the solvent remaining in the material is removed using a combination of steam (direct and indirect) and vacuum. The solvent vapourises and is condensed in the solvent condensate. The mixture of solvent and water is separated in the solvent water separator tank by a gravity process. When the extracted material is free of solvent it is discharged through the door at the base of the extractor.
- Desolventising miscella: Miscella is a mixture of solvent and oil from the extraction material which accumulates in the miscella tank during the extraction process. The solvent and oil are separated using a combination of steam (direct and indirect) and vacuum.
This Computer Controlled Unit is supplied with the EDIBON Computer Control System (SCADA), and includes: The unit itself + a Control Interface Box + a Data Acquisition Board + Computer Control, Data Acquisition and Data Management Software Packages, for controlling the process and all parameters involved in the process.
Des exercices et pratiques guidées
EXERCICES GUIDÉS INCLUS DANS LE MANUEL
- Operation of small scale version of industrial processes.
- Effect of degree of pretreatment of solid material on extraction efficiency.
- Effect of extraction time.
- Effect of drain time.
- Effect of solvent type.
- Effect of solvent percolation rate.
- Effect of process temperature.
- Effect of process pressure.
- Method of solvent recovery.
- Degree of solvent recovery.
- Sensors calibration.
PLUS D'EXERCICES PRATIQUES À EFFECTUER AVEC CETTE ÉQUIPEMENT
- Many students view results simultaneously. To view all results in real time in the classroom by means of a projector or an electronic whiteboard.
- Open Control, Multicontrol and Real Time Control. This unit allows intrinsically and/or extrinsically to change the span, gains, proportional, integral, derivate parameters, etc, in real time.
- The Computer Control System with SCADA allows a real industrial simulation.
- This unit is totally safe as uses mechanical, electrical and electronic, and software safety devices.
- This unit can be used for doing applied research.
- This unit can be used for giving training courses to Industries even to other Technical Education Institutions.
- Control of the QEDC unit process through the control interface box without the computer.
- Visualization of all the sensors values used in the QEDC unit process.
- By using PLC-PI additional 19 more exercises can be done.
- Several other exercises can be done and designed by the user.
EQUIPEMENT COMPLEMENTAIRE
Unité d´Extraction Liquide/Liquide
Usine Pilote d'Extraction Solide-Liquide, Contrôlée par Ordinateur (PC) et Écran Tactile
Unité d´Extraction Solide/Liquide, Contrôlée par Ordinateur (PC)
Unité d´Extraction Solide/Liquide
Unité pour l'Étude de l'Écoulement dans les Colonnes de Remplissage, Contrôlée par Ordinateur (PC)
Qualité
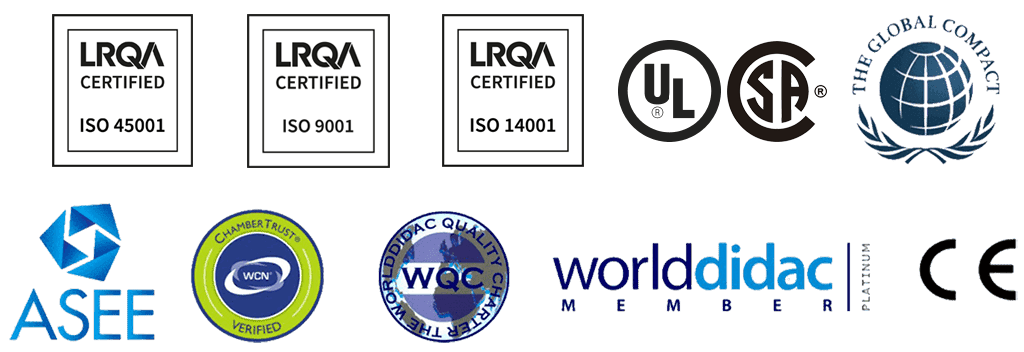
Service après vente
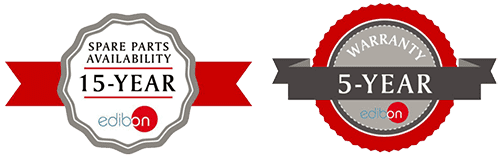