TCRC Peralatan Demonstrasi Siklus Refrigerasi, Dikendalikan dari Komputer (PC)
SISTEM INOVATIF
The Computer Controlled Refrigeration Cycle Demonstration Unit, "TCRC", makes it possible to visualize clearly all the processes of a compression cooling system and the heat pump cycle, the analysis and demonstration of the pressure-temperature relationship during evaporation and condensation processes, the influence of diverse parameters on the process, etc.
Ekspansi
Laboratorium
BERITA TERKAIT
GAMBARAN UMUM
The Computer Controlled Refrigeration Cycle Demonstration Unit, "TCRC", allows the demonstration of vapour compression refrigeration and heat pump cycle with visual observation of all important processes.
Thanks by utilising a non-toxic refrigerant fluid with a low vapour pressure (SES36 refrigerant, environmental friendly), the evaporation and condensation processes are clearly visible in the glass cylinders (evaporator and condenser).
The evaporator is a vertical cylinder, made of glass, containing SES36, closed on both ends. Into the glass cylinder there is a niquel-plated copper coil.
Hermetic compressor draws vapour from the evaporator and compresses this before discharging it to the condenser. The low pressure of the evaporator causes the refrigerant to boil. The water flowing through the coil heats the refrigerant causing the vapours generation and the water temperature decreases.
From the compressor the high pressure vapour passes to the condenser.
The condenser, as the evaporator, is a glass recipient closed on both ends with a nickel-plated copper coil into it. Vapour condenses on the surface of the coil and falls to the bottom of the condenser. The liberated heat by the refrigerant phase change is transferred to the cooling water flowing through the coil.
The float valve located at the base of the condenser, that works as an expansion valve, controls the flow of high pressure refrigerant liquid returning to the evaporator. The refrigerant, after passing through the floating valve, expands to form a liquid vapour mixture at the same pressure as the evaporator and the cycle is repeated.
Besides, an insulating valve is installed in the condenser inferior part that can be closed for the demonstration of the technique used in the maintenance of refrigeration installations, whether commercial or industrial, where the refrigerant is collected and stored in the condenser. This technique is important for demonstrating how to prevent a possible refrigerant gas leak during the maintenance operations.
The unit allows a safe operation since it includes different safety elements, such as a high pressure switch that turns off the compressor when the pressure in the condenser and at the condenser upper part, the unit has a relief valve that opens itself when the condenser pressure is higher than the maximum valve allowed.
By adjustment of the water flow to the evaporator and condenser coils, using control valves, the condensing and evaporating pressures can be varied.
We can control the unit and know, at any time, the measure of:
- The temperature and pressure of the refrigerant fluid in the evaporator and in the condenser.
- The temperature of the compression and expansion processes.
- The temperature of the water inlet and outlet at the coils of the evaporator and condenser.
- The water flow in the two coils.
- The room temperature.
- The electrical power used in the compression stage.
This Computer Controlled Unit is supplied with the EDIBON Computer Control System (SCADA), and includes: The unit itself + a Control Interface Box + a Data Acquisition Board + Computer Control, Data Acquisition and Data Management Software Packages, for controlling the process and all parameters involved in the process.
LATIHAN DAN PRAKTEK PEDOMAN
LATIHAN PRAKTIS YANG DIANDAL TERMASUK DALAM PANDUAN
- Demonstration of the vapour compression refrigeration and heat pump cycle and visualization of the most important processes.
- Relation between pressure and temperature.
- Demonstration of the refrigerant transfer from the evaporator to the condenser.
- Charging demonstration.
- Demonstration of the air effect in a refrigeration (cooling) system.
- Evaporation and condensation temperatures effect in the refrigeration (cooling) rate and in the heat transfer at the condenser.
- Analysis of the pressures relation effect in the system behaviour.
- Determination of the system operation coefficients: coefficient of working as a refrigerator and as a heat pump.
- Measurement of the electrical power.
- Estimation of the heat transmission global coefficient between the SES36 refrigerant and the water.
- Sensors calibration.
LEBIH BANYAK LATIHAN PRAKTIS YANG AKAN DILAKUKAN DENGAN UNIT
- Many students view results simultaneously. To view all results in real time in the classroom by means of a projector or an electronic whiteboard.
- Open Control, Multicontrol and Real Time Control. This unit allows intrinsically and/or extrinsically to change the span, gains: proportional, integral, derivate parameters, etc, in real time.
- The Computer Control System with SCADA allows a real industrial simulation.
- This unit is totally safe as uses mechanical, electrical and electronic, and software safety devices.
- This unit can be used for doing applied research.
- This unit can be used for giving training courses to Industries even to other Technical Education Institutions.
- Control of the TCRC unit process through the control interface box without the computer.
- Visualization of all the sensors values used in the TCRC unit process.
- By using PLC-PI additional 19 more exercises can be done.
- Several other exercises can be done and designed by the user.
PERALATAN SIMILAR TERSEDIA
PERALATAN KOMPLEMENTER
Menara Pendingin Meja, Dikendalikan dari Komputer (PC)
Menara Pendingin Meja
Peralatan Demonstrasi Siklus Refrigerasi
Peralatan Pendinginan dengan Absorpsi, Dikendalikan dari Komputer (PC)
Peralatan Pendinginan dengan Absorpsi
Pengaturan Daya dan Kesalahan pada Sistem Pendingin, Dikendalikan dari Komputer (PC)
Peralatan Pendinginan dengan Tabung Vortex, Dikendalikan dari Komputer (PC)
Pompa Panas Termoelektrik, Dikendalikan dari Komputer (PC)
Peralatan Sistem Pendinginan dengan Kompresi Sederhana
Pompa Panas + AC + Pendinginan Terbalik dengan 2 kondensor dan 2 evaporator (Air/UDara), Dikendalikan dari Komputer (PC)
Pompa Panas + AC + Pendinginan Terbalik dengan 2 kondensor dan 2 evaporator (Air/UDara)
Pompa Panas + AC + Pendinginan Terbalik dengan 4 kondensor dan 4 evaporator (Air/UDara), Dikendalikan dari Komputer (PC)
KUALITAS
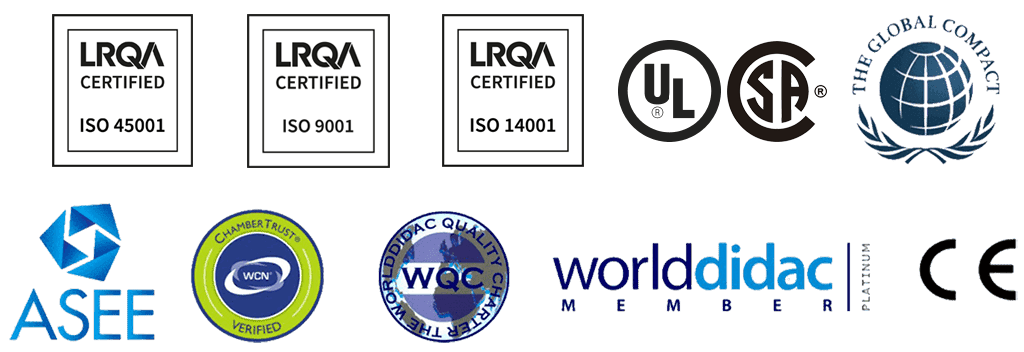
LAYANAN PURNA JUAL
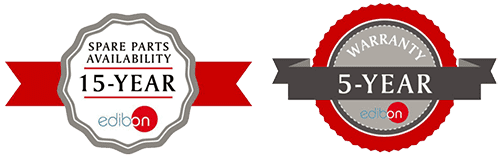