TICC Sistem Pelatihan Penukar Panas, Dikendalikan dari Komputer (PC)
SISTEM INOVATIF
The Computer Controlled Heat Exchangers Training System, "TICC", has been designed by EDIBON to study and compare different types of small-scale heat exchangers working with parallel or counterflow arrangements.
Laboratorium
BERITA TERKAIT
GAMBARAN UMUM
The Computer Controlled Heat Exchangers Training System, "TICC", has been designed by EDIBON to study and compare different types of small-scale heat exchangers working with parallel or counterflow arrangements.
The minimum supply consists of two main elements: the Base Service Unit, "TIUS", and at least one of the required elements described below.
The Base Service Unit, "TIUS", has the following functions:
- Heating water in a computer controlled thermostatic bath.
- Pumping the hot water.
- Regulation and measurement of the cold water and hot water flows.
- Measurement of the inlet and outlet temperatures of the cold water and the hot water.
- Measurement of the pressure drop in the exchanger.
Required elements (at least one) (Not included):
- TITC. Concentric Tube Heat Exchanger for TICC: It has been designed to study the heat transfer between hot water flowing through an internal tube and cold water flowing through the annular area between the internal and the external tubes.
- TITCA. Extended Concentric Tube Heat Exchanger for TICC: It has been designed to study the heat transfer between hot water flowing through an internal tube and cold water flowing through the annular area between the internal and the external tubes.
- TIPL. Plate Heat Exchanger for TICC: It has been designed to study the heat transfer between hot water and cold water flowing through alternate channels formed between parallel plates.
- TIPLA. Extended Plate Heat Exchanger for TICC: It has been designed to study the heat transfer between hot water and cold water flowing through alternate channels formed between parallel plates.
- TICT. Shell and Tube Heat Exchanger for TICC: It consists of a series of tubes inside the heat exchanger where hot water flows. The cooling water flows through the space between the inner tubes and the shell.
- TIVE. Jacketed Vessel Heat Exchanger for TICC: Allows the study of heat transfer between hot water flowing through a jacket and the cold water contained in a vessel.
- TIVS. Coil Vessel Heat Exchanger for TICC: Allows the study of heat transfer between hot water flowing through a coil and cold watercontained in the vessel.
- TIFT. Turbulent Flow Heat Exchanger for TICC: Let us study the heat transfer between hot water that circulates through an internal tubeand cold water that flows through the annular zone between the internal and the external tube.
- TICF. Cross Flow Heat Exchanger for TICC: Designed to study heat transfer between two fluids in cross flow configuration. Hot water flow coming from the base unit enters and leaves a radiator perpendicular to an air current, which is generated by a fan.
This Computer Controlled Unit is supplied with the EDIBON Computer Control System (SCADA), and includes: The unit itself + aControl Interface Box + a Data Acquisition Board + Computer Control, Data Acquisition and Data Management Software Packages, for controlling the process and all parameters involved in the process.
Aksesoris
Penukar Panas Pelat untuk TICC
Penukar Panas Shell dan Tabung untuk TICC
Penukar Panas Tabung Konsentris untuk TICC
Unit Dasar dan Layanan (Umum untuk Semua Penukar Panas Jenis "TI" yang Tersedia)
Penukar Panas Wadah Berjaket untuk TICC
Penukar Panas Wadah Berjaket dengan Koil untuk TICC
Penukar Panas Tabung Konsentris yang Diperluas untuk TICC
Penukar Panas Pelat yang Diperluas untuk TICC
Penukar Panas Aliran Silang untuk TICC
LATIHAN DAN PRAKTEK PEDOMAN
LATIHAN PRAKTIS YANG DIANDAL TERMASUK DALAM PANDUAN
Practices to be done with the Concentric Tube Heat Exchanger for TICC (TITC):
- Global energy balance in the heat exchanger and the study of losses.
- Exchanger effectiveness determination. NTU Method.
- Study of the heat transfer under counter-current and co-current flow conditions.
- Flow influence on the heat transfer. Reynolds number calculation.
Practices to be done with the Extended Concentric Tube Heat Exchanger for TICC (TITCA):
- Global energy balance in the heat exchanger and the study of losses.
- Exchanger effectiveness determination. NTU Method.
- Study of the heat transfer under counter-current and co-current flow conditions.
- Flow influence on the heat transfer. Reynolds number calculation.
Practices to be done with the Plate Heat Exchanger for TICC (TIPL):
- Global energy balance in the heat exchanger and the study of losses.
- Exchanger effectiveness determination. NTU Method.
- Study of the heat transfer under counter-current and co-current flow conditions.
- Flow influence on the heat transfer. Reynolds number calculation.
Practices to be done with the Extended Plate Heat Exchanger for TICC (TIPLA):
- Global energy balance in the heat exchanger and the study of losses.
- Exchanger effectiveness determination. NTU Method.
- Study of the heat transfer under counter-current and co-current flow conditions.
- Flow influence on the heat transfer. Reynolds number calculation.
Practices to be done with the Shell and Tube Heat Exchanger for TICC (TICT):
- Global energy balance in the heat exchanger and the study of losses.
- Exchanger effectiveness determination. NTU Method.
- Study of the heat transfer under counter-current and co-current flow conditions.
- Flow influence on the heat transfer. Reynolds number calculation.
Practices to be done with the Jacketed Vessel Heat Exchanger for TICC (TIVE):
- Global balance of energy in the heat exchanger and losses study.
- Determination of the exchanger effectiveness. NTU Method.
- Influence of the flow on the heat transfer. Calculation of the number of Reynolds.
- Influence of the vessel stirring on the heat transfer when operating in batches.
- Influence of the vessel’s water volume on the heat transfer when operating in batches.
Practices to be done with the Coil Vessel Heat Exchanger for TICC (TIVS):
- Global balance of energy in the heat exchanger and the study of losses.
- Determination of the exchanger effectiveness. NTU Method.
- Influence of the flow on the heating transfer. Calculation of Reynolds number.
- Influence of the stirring vessel on the heat transfer with operation in batches.
- Influence of the water volume in the vessel on the heat transfer with operation in batches.
Practices to be done with the Turbulent Flow Heat Exchanger for TICC (TIFT):
- Global energy balance in the heat exchanger and loss study.
- Determination of the exchanger effectiveness. NTU Method.
- Study of the heat transfer in counter-current and co-current flow conditions.
- Flow influence on heat transfer. Reynolds number calculation.
- Obtaining of the correlation that relates Nusselt number with Reynolds number and Prandtl number.
- Obtaining of the heat transfer coefficients by convection.
Practices to be done with the Cross Flow Heat Exchanger for TICC (TICF):
- Introduction to the concept of psychometric properties.
- Effect of temperature differential on the heat transfer coefficient.
- Familiarization with cross flow heat exchanger.
- Overall energy balance in the heat exchanger and study of losses.
- Determination of the exchanger effectiveness (NTU method).
- Influence of air and water flow on the heat transfer. Reynolds number calculation.
LEBIH BANYAK LATIHAN PRAKTIS YANG AKAN DILAKUKAN DENGAN UNIT
- Sensors calibration.
- Study of the hysteresis in the flow sensors.
- Many students view results simultaneously. To view all results in real time in the classroom by means of a projector or an electronic whiteboard.
- Open Control, Multicontrol and Real Time Control. This unit allows intrinsically and/or extrinsically to change the span, gains, proportional, integral, derivative parameters, etc, in real time.
- The Computer Control System with SCADA and PID Control allow a real industrial simulation.
- This unit is totally safe as uses mechanical, electrical and electronic, and software safety devices.
- This unit can be used for doing applied research.
- This unit can be used for giving training courses to Industries even to other Technical Education Institutions.
- Control of the TICC unit process through the control interface box without the computer.
- Visualization of all the sensors values used in the TICC unit process.
- By using PLC-PI additional 19 more exercises can be done.
- Several other exercises can be done and designed by the user.
PERALATAN SIMILAR TERSEDIA
Sistem Pelatihan Penukar Panas
Peralatan Dasar Penukar Panas, Dikendalikan dari Komputer (PC)
PERALATAN KOMPLEMENTER
Unit Dasar dan Layanan (Umum untuk Semua Penukar Panas Jenis "TI" yang Tersedia)
Penukar Panas Tabung Konsentris untuk TICC
Penukar Panas Tabung Konsentris yang Diperluas untuk TICC
Penukar Panas Pelat untuk TICC
Penukar Panas Pelat yang Diperluas untuk TICC
Penukar Panas Shell dan Tabung untuk TICC
Penukar Panas Wadah Berjaket untuk TICC
Penukar Panas Wadah Berjaket dengan Koil untuk TICC
Penukar Panas Aliran Turbulen untuk TICC
Penukar Panas Aliran Silang untuk TICC
Sistem Pelatihan Penukar Panas
Unit Dasar dan Layanan (Umum untuk Semua Penukar Panas Jenis "TI..B" yang Tersedia)
KUALITAS
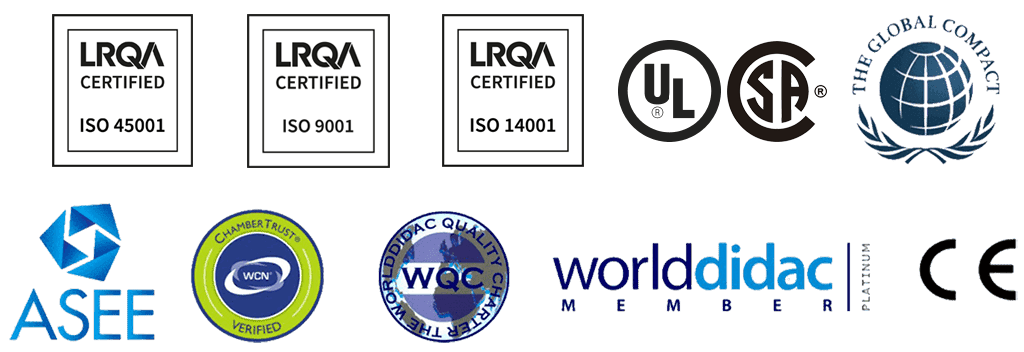
LAYANAN PURNA JUAL
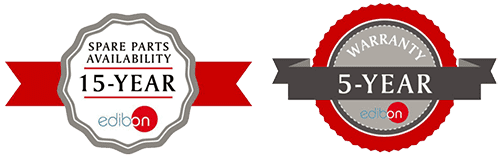