TMSC Mesin Stirling, Dikendalikan dari Komputer (PC)
SISTEM INOVATIF
The Computer Controlled Stirling Motor, "TMSC", is used to demonstrate the operation of a thermodynamic machine for the conversion of energy.
Ekspansi
Laboratorium
BERITA TERKAIT
GAMBARAN UMUM
The Computer Controlled Stirling Motor, "TMSC", is used to demonstrate the operation of a thermodynamic machine for the conversion of energy. It converts thermal energy into mechanical energy and operates as a motor (heat engine). Additionally it can operate an electrical generator and load.
An ideal stirling cycle has four phases:
- Phase 1: Constant volume heating of the gas in the hot cylinder.
- Phase 2: Isothermal expansion at constant temperature in the hot cylinder.
- Phase 3: Constant volume working in the cold cylinder.
- Phase 4: Isothermal compression of the gas in the cold cylinder.
The Computer Controlled Stirling Motor, "TMSC", unit designed by EDIBON is an Alfa type engine. It consists of two power pistons located in separate cylinders (one for the cold source and another for the hot one). They are connected to a tube where the regenerator is located, which stores and transfers the heat, that enables the engine to reach a higher efficiency.
Gas moves between both cylinders in a close circuit. The external source provides energy to the hot cylinder, generating the expansion of the gas, and the subsequent motion of the piston, 90° out of phase from the other, and connected to it by a crankshaft.
The hot gas passes to the cold cylinder. During this time the cold cylinder piston compresses the cooled gas and forces it to move to the hot cylinder, where it receives the heat from the hot source and the cycle starts again.
The unit also includes a braking system with force sensor and an electrical generator with pulley to convert the mechanical energy into electrical energy, equipped with an electrical load and current and voltage measurement system.
This unit is supplied with the suitable sensors and instrumentation for the control and measurement of the most representative parameters, as:
Flame control. Temperatures measurement in the cylinders. Pressures measurement in the cylinders. Speed measurement (rpm). Torque measurement (force). Current and voltage measurement. Stirling motor power generated and efficiency calculation.
This Computer Controlled Unit is supplied with the EDIBON Computer Control System (SCADA), and includes: The unit itself + aControl Interface Box + a Data Acquisition Board + Computer Control, Data Acquisition and Data Management Software Packages, forcontrolling the process and all parameters involved in the process.
LATIHAN DAN PRAKTEK PEDOMAN
LATIHAN PRAKTIS YANG DIANDAL TERMASUK DALAM PANDUAN
- Study of the conversion of thermal-mechanical-electrical energy.
- Study of the relationship between the temperatures difference of the thermal machine and the speed generated.
- Calculation of the threshold temperatures difference which generates motion.
- Study of the mechanical power in relation to speed.
- Study of the electrical power in relation to speed.
- Mechanical efficiency calculation.
- Electrical efficiency calculation.
- Speed measurement (rpm).
- Torque measurement.
- Measurement of the generated electrical power.
- Temperature measurements.
- Pressure measurements.
- Sensors calibration.
LEBIH BANYAK LATIHAN PRAKTIS YANG AKAN DILAKUKAN DENGAN UNIT
- Many students view results simultaneously. To view all results in real time in the classroom by means of a projector or an electronic whiteboard.
- Open Control, Multicontrol and Real Time Control. This unit allows intrinsically and/or extrinsically to change the span, gains, proportional, integral, derivative parameters, etc, in real time.
- The Computer Control System with SCADA and PID Control allow a real industrial simulation.
- This unit is totally safe as uses mechanical, electrical and electronic, and software safety devices.
- This unit can be used for doing applied research.
- This unit can be used for giving training courses to Industries even to other Technical Education Institutions.
- Control of the TMSC unit process through the control interface box without the computer.
- Visualization of all the sensors values used in the TMSC unit process.
- By using PLC-PI additional 19 more exercises can be done.
- Several other exercises can be done and designed by the user.
PERALATAN SIMILAR TERSEDIA
PERALATAN KOMPLEMENTER
Pompa Panas Termoelektrik, Dikendalikan dari Komputer (PC)
KUALITAS
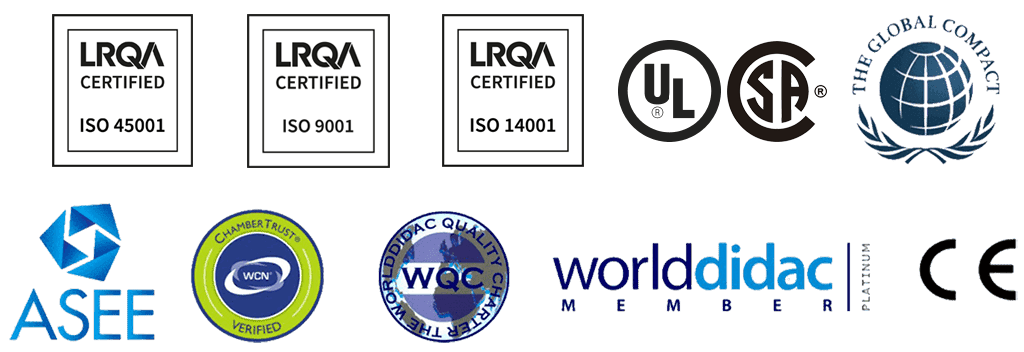
LAYANAN PURNA JUAL
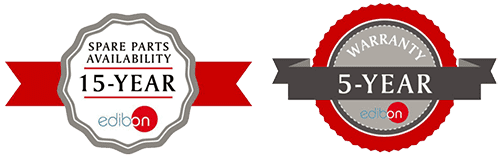