At EDIBON, we are committed to strengthening skills as a strategic pillar for the competitiveness and social well-being of the European Union. Proper training not only boosts the economy but also enables individuals to fully participate in society and democracy.
AE-PLC-FMS1 輸送、組立、プレス、選別、ねじ締め、保管のためのフレキシブル製造システム
革新的なシステム
The Flexible Manufacturing System for Transport, Assembly, Pressing, Selection, Screwing, and Storage, "AE-PLC-FMS1", designed by EDIBON, enables the study and practice of an automated production cycle consisting of 9 distinct workstations. This system integrates all the mentioned workstations, as well as an additional parts feeding workstation, a robotic arm, and a transport station to ensure comprehensive system operation.
関連ニュース
概要
The Flexible Manufacturing System for Transport, Assembly, Pressing, Selection, Screwing, and Storage, "AE-PLC-FMS1", is a highly adaptable and configurable system designed for the study and application of advanced automation principles within the context of Industry 4.0 and Industry 5.0. This unit integrates key technologies such as automated control, inter-device networking through smart networks, PLC programming of assembly lines, and real-time data analysis, allowing users to explore the capabilities of digitized and connected manufacturing that characterize the Fourth Industrial Revolution and pave the way for the Fifth Industrial Revolution.
It consists of nine interconnected workstations that perform specific tasks, including feeding, assembly, verification, pressing, mounting, and storing (dimension, material, and color) parts. Each of these workstations requires its own PLC from the selected brand (PANASONIC, SIEMENS, ALLEN BRADLEY, MITSUBISHI and/or OMRON), allowing users to explore how advanced control and production concepts are applied in an automated manufacturing line. The workflow is coordinated by a central PLC system (from the same brand chosen for the stations) and an Ethernet network, making the "AE-PLC-FMS1" a comprehensive learning resource for those interested in automation engineering and flexible manufacturing.
The included workstations are:
- Part Feeding Workstation, "AE-PLC-A": Initiates the cycle by moving base parts from the waiting position onto the conveyor belt.
- Linear Transport Workstation, "AE-PLC-T": Receives parts from the storage station and positions them for transfer to the next station.
- Mounting Workstation "AE-PLC-M": Adds a second part to the base, verifying dimensions before proceeding.
- Automatic Pressing Workstation "AE-PLC-P": Uses a hydraulic cylinder to secure parts together, consolidating the base and additional components.
- Rotary Table Workstation: Feeding, Quality Control and Assembly (dimensional study), "AE-PLC-MR1": Performs dimensional verification of parts.
- Rotary Table Workstation: Feeding, Quality Control, and Assembly (material and color study), "AE-PLC-MR2": Checks the part’s material and color for quality.
- Automatic Screwdriving Workstation, "AE-PLC-AT": Places four screws into the base parts for completion.
- Robotic Arm Workstation, "AE-BR": Performs the screwing process with an integrated automatic drill.
- Storage Workstation, "AE-PLC-AL": Picks up the base parts with an automatic handler and places them in the designated storage area.
The system allows students and instructors to delve into fundamental concepts of industrial automation. Through its use, students acquire practical skills in designing and operating automated systems, gaining a deep understanding of the coordinated work across the various workstations of a real production line. This configurable system has been carefully designed so that each of its workstations performs specific functions that simulate real industrial processes.
演習と指導の慣行
マニュアルに含まれるガイド付き実習
Practical possibilities to be done with the Flexible Manufacturing System for Transport, Assembly, Pressing, Selection, Screwing, and Storage (AE-PLC-FMS1):
- Introduction to flexible manufacturing system (FMS).
- Introduction to pneumatics and electro-pneumatics.
- Introduction to vacuum technology.
- Study of the sensor detection.
- Testing the digital inputs and outputs of the automatic system through a PLC.
- Modify manufacturing parameters through the PLC.
- Configuration of a pneumatic application.
- Introduction to the Human-machine interface systems (HMI).
- Study of an automatic control of an industrial system.
- Control of the flexible manufacturing system through a central PLC in an Ethernet network with local PLC in each workstation.
- Manage the flexible manufacturing system through the HMI device.
Practical possibilities to be done with the workstation alone:- Part Feeding Workstation (AE-PLC-A).
- Manual control of a Feeding system.
- Automatic control of a Feeding system.
- Change the parameters of the Feeding process.
- Optimize the process time.
- Study and analysis of the faults inserted in the process with the fault generation module.
- Linear Transport Workstation (AE-PLC-T).
- Manual control of a transporting system.
- Automatic control of a transporting system.
- Change the parameters of a transporting process.
- Optimize the process time.
- Study and analysis of the faults inserted in the process with the fault generation module.
- Mounting Workstation (AE-PLC-M).
- Manual control of a mounting system.
- Automatic control of a mounting system.
- Change the parameters of the mounting process.
- Optimization of the process time.
- Study and analysis of the faults inserted in the process with the fault generation module.
- Automatic Pressing Workstation (AE-PLC-P).
- Manual control of a pressing system.
- Automatic control of a pressing system.
- Change the parameters of the pressing process.
- Optimization of the process time.
- Study and analysis of the faults inserted in the process with the fault generation module.
- Rotary Table Workstation: Feeding, Quality Control and Assembly(dimensional study) (AE-PLC-MR1).
- Introduction to the flexible manufacturing system: Identification of unit components.
- Introduction to pneumatics and electro-pneumatics: Identification of components.
- Configuration of a pneumatic application.
- Operation of pneumatic system: Introduction to vacuum technology and pneumatic actuators.
- Study of sensor detection.
- Manual control of a rotary table.
- Automatic control of a rotary table.
- Industrial application example.
- Industrial application tuning.
- Fault inserted analysis and diagnosis.
- Rotary Table Workstation: Feeding, Quality Control, and Assembly (material and color study) (AE-PLC-MR2).
- Manual control of the rotary table system.
- Manual control of the quality control and drilling process on a rotary table.
- Automatic control of the rotary table system.
- Automatic control of the quality control and drilling process on a rotary table.
- Change the parameters of the rotary table process.
- Optimize the process time.
- Study and analysis of the faults inserted in the process with the fault generation module.
- Automatic Screwdriving Workstation (AE-PLC-AT).
- Manual control of a screwing system.
- Automatic control of a screwing system.
- Change the parameters of the screwing process.
- Optimize the process time.
- Study and analysis of the faults inserted in the process with the fault generation module.
- Robotic Arm Workstation (AE-BR).
- Introduction to robotic systems.
- Robotic arm configuration.
- Set a simple movement of the robotic arm.
- Configuration of a pneumatic application.
- Set a simple pick and place task with the robotic arm.
- Modification of the task parameters.
- Optimize the task time.
- Storage Workstation (AE-PLC-AL).
- Manual control of a storing system.
- Automatic control of a storing system.
- Change the parameters of the storing process.
- Optimize the process time.
- Study and analysis of the faults inserted in the process with the fault generation module.
Practical possibilities to be done with the optional software Automation Systems Simulation Software (AE-AS):
- Introduction to the SCADA control system.
- OPC server system with Ethernet.
- SCADA control of an automatic industrial system through PC.
利用可能な類似の機器
6.2.6.- PLCを使用した柔軟な製造システム
AE-PLC-FMS2
The Flexible Manufacturing System for Transport, Assembly, Selection, Screwing, and Storage, "AE-PLC-FMS2", is a highly adaptable and configurable system designed for the study and application of advanced automation principles within the context...
6.2.6.- PLCを使用した柔軟な製造システム
AE-PLC-FMS3
輸送、組立、選別(素材と色)、保管のためのフレキシブル製造システム
The Flexible Manufacturing System for Transport, Assembly, Selection (Material and Color), and Storage, "AE-PLC-FMS3", is a highly adaptable and configurable system designed for the study and application of advanced automation principles within...
6.2.6.- PLCを使用した柔軟な製造システム
AE-PLC-FMS4
ろ過、混合、産業プロセス管理、瓶詰めのためのフレキシブル製造システム
The Flexible Manufacturing System for Filtering, Mixing, Industrial Process Control, and Bottling, "AE-PLC-FMS4", is a highly adaptable and configurable system designed for the study and application of advanced automation principles within the...
6.2.6.- PLCを使用した柔軟な製造システム
AE-PLC-FMS5
輸送、分類、選別、空気圧処理のためのフレキシブル製造システム
Flexible Manufacturing System for Transport, Classification, Selection, and Pneumatic Handling, "AE-PLC-FMS5," is a highly adaptable and configurable system designed for the study and application of advanced automation principles within the...
6.2.6.- PLCを使用した柔軟な製造システム
AE-PLC-FMS6
供給と分類のためのフレキシブル製造システム
The Flexible Manufacturing System for Feeding and Classification, "AE-PLC-FMS6", is a highly adaptable and configurable system designed for the study and application of advanced automation principles within the context of Industry 4.0 and Industry...
6.2.6.- PLCを使用した柔軟な製造システム
AE-PLC-FMS7
供給、識別、分類、輸送のためのフレキシブル製造システム
The Flexible Manufacturing System for Feeding, Identification, Classification, and Transport, "AE-PLC-FMS7", is a highly adaptable and configurable system designed for the study and application of advanced automation principles within the context...
6.2.6.- PLCを使用した柔軟な製造システム
AE-PLC-FMS14
産業プロセス管理、充填、シールおよび保管のためのフレキシブル製造システム
The Flexible Manufacturing System for Industrial Process Control, Filling, Sealing, and Storage, "AE-PLC-FMS14", is a highly adaptable and configurable system designed for the study and application of advanced automation principles within the...
6.2.6.- PLCを使用した柔軟な製造システム
AE-PLC-FMS15
供給、組立、ロボット処理および輸送のためのフレキシブル製造システム
The Flexible Manufacturing System for Feeding, Assembly, Robotic Handling, and Transport, "AE-PLC-FMS15", is a highly adaptable and configurable system designed for the study and application of advanced automation principles within the context of...
補完的な機器
6.2.6.- PLCを使用した柔軟な製造システム
AE-PLC-FMS2
輸送、組立、選別、ねじ締め、保管のためのフレキシブル製造システム
The Flexible Manufacturing System for Transport, Assembly, Selection, Screwing, and Storage, "AE-PLC-FMS2", is a highly adaptable and configurable system designed for the study and application of advanced automation principles within the context...
6.2.6.- PLCを使用した柔軟な製造システム
AE-PLC-FMS3
輸送、組立、選別(素材と色)、保管のためのフレキシブル製造システム
The Flexible Manufacturing System for Transport, Assembly, Selection (Material and Color), and Storage, "AE-PLC-FMS3", is a highly adaptable and configurable system designed for the study and application of advanced automation principles within...
6.2.6.- PLCを使用した柔軟な製造システム
AE-PLC-FMS4
ろ過、混合、産業プロセス管理、瓶詰めのためのフレキシブル製造システム
The Flexible Manufacturing System for Filtering, Mixing, Industrial Process Control, and Bottling, "AE-PLC-FMS4", is a highly adaptable and configurable system designed for the study and application of advanced automation principles within the...
6.2.6.- PLCを使用した柔軟な製造システム
AE-PLC-FMS5
輸送、分類、選別、空気圧処理のためのフレキシブル製造システム
Flexible Manufacturing System for Transport, Classification, Selection, and Pneumatic Handling, "AE-PLC-FMS5," is a highly adaptable and configurable system designed for the study and application of advanced automation principles within the...
6.2.6.- PLCを使用した柔軟な製造システム
AE-PLC-FMS6
供給と分類のためのフレキシブル製造システム
The Flexible Manufacturing System for Feeding and Classification, "AE-PLC-FMS6", is a highly adaptable and configurable system designed for the study and application of advanced automation principles within the context of Industry 4.0 and Industry...
6.2.6.- PLCを使用した柔軟な製造システム
AE-PLC-FMS7
供給、識別、分類、輸送のためのフレキシブル製造システム
The Flexible Manufacturing System for Feeding, Identification, Classification, and Transport, "AE-PLC-FMS7", is a highly adaptable and configurable system designed for the study and application of advanced automation principles within the context...
6.2.6.- PLCを使用した柔軟な製造システム
AE-PLC-FMS14
産業プロセス管理、充填、シールおよび保管のためのフレキシブル製造システム
The Flexible Manufacturing System for Industrial Process Control, Filling, Sealing, and Storage, "AE-PLC-FMS14", is a highly adaptable and configurable system designed for the study and application of advanced automation principles within the...
6.2.6.- PLCを使用した柔軟な製造システム
AE-PLC-FMS15
供給、組立、ロボット処理および輸送のためのフレキシブル製造システム
The Flexible Manufacturing System for Feeding, Assembly, Robotic Handling, and Transport, "AE-PLC-FMS15", is a highly adaptable and configurable system designed for the study and application of advanced automation principles within the context of...
品質
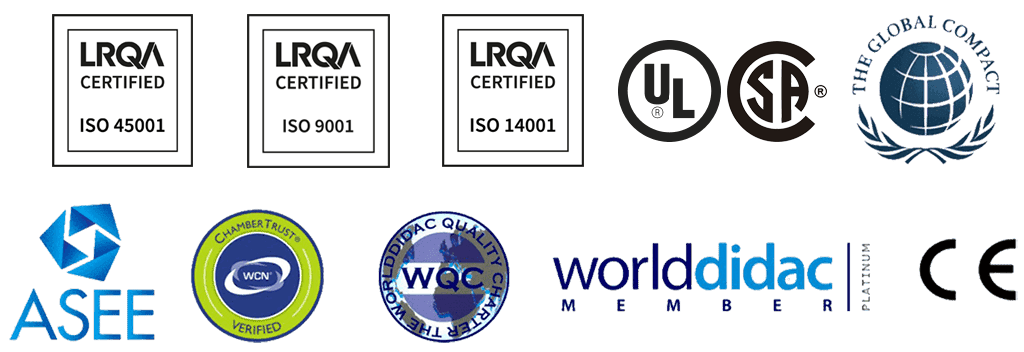
アフターサービス
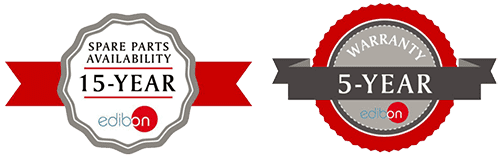