At EDIBON, we are committed to strengthening skills as a strategic pillar for the competitiveness and social well-being of the European Union. Proper training not only boosts the economy but also enables individuals to fully participate in society and democracy.
BS-PLC PLC制御のセンサースタディモジュール
革新的なシステム
The Modular System for the Study of Sensors with PLC Control, "PLC-BS", are a large number of modules that show the operation of different sensors to understand the sensor control applications of different technologies, applied to common measurement and control systems such as temperature, flow, pressure, deformation, velocity, etc.
関連ニュース
概要
The Modular System for the Study of Sensors with PLC Control, "PLC-BS", are a large number of modules that show the operation of different sensors to understand the sensor control applications of different technologies, applied to common measurement and control systems such as temperature, flow, pressure, deformation, velocity, etc. The "PLC-BS" are designed to work with PLC control and offer an introduction to PLC units that work with a sensor signal and control an actuator.
The "PLC-BS" modules, designed by EDIBON, allow the user to learn about the basic concepts of different sensors (operation, sensor calibration, etc.) and the basic operation of a Programmable Logic Control (PLC) unit without any previous knowledge or experience.
付属品
6.2.3.- PLCによる計装と制御
BS2-PLC
The "BS2-PLC" has been designed to study the use and applications of temperature sensors as a measure device and how to perform a temperature control through a PLC. TThe unit has a half-open space inside which there is a lamp that heats the...
6.2.3.- PLCによる計装と制御
BS3-PLC
PLC用圧力試験モジュール
The "BS3-PLC" has been designed to study the pressure measurement techniques and control application with a PLC. This unit is equipped with a pressure chamber with several sensors, with different uses and applications, adjusted to measure the...
6.2.3.- PLCによる計装と制御
BS4-PLC
PLC用流量試験モジュール
The "BS4-PLC" has been designed to study the flow measurement techniques and control with PLC. This unit is unit with two tanks assembled on a structure with a pumping system that allows pumping the water from the reservoir tank, through the...
6.2.3.- PLCによる計装と制御
BS5-PLC
PLC用炉の試験モジュール
The "BS5-PLC" has been designed to study the temperature measurement techniques inside a sealed place, such as an oven and how to perform a temperature control through a PLC. This unit is equipped with an oven that contains a heating element and a...
6.2.3.- PLCによる計装と制御
BS6-PLC
PLC用液面試験モジュール
The "BS6-PLC" has been designed to study the liquid level measurement and control techniques of a tank through a PLC. This unit is unit with two tanks with sensor of different technology for level measurement. One of the level sensor output...
6.2.3.- PLCによる計装と制御
BS7-PLC
PLC用タコメーター試験モジュール
The "BS7-PLC" has been designed to study the linear and angular speed measurement techniques through a PLC. This unit is unit with a miniature motor to move an axle at different speeds, being able to adjust de motor speed by changing the voltage...
6.2.3.- PLCによる計装と制御
BS9-PLC
PLC用空気圧試験モジュール
The "BS9-PLC" has been designed to study the control and handling techniques of a pneumatic actuator through a PLC. The actuator is a double acting pneumatic cylinder that allows moving a platform. The displacement of the piston axle is detected...
6.2.3.- PLCによる計装と制御
BS10-PLC
PLC用照明試験モジュール
The "BS10-PLC" has been designed to study different light measurement techniques and control light intensity through a PLC. This unit is composed of a lamp whose intensity can be controlled according to the voltage applied and a series of...
演習と指導の慣行
マニュアルに含まれるガイド付き実習
Practical exercises with PLC-BS2:
- How to use the Curie effect as application of a high temperature thermostatic controller.
- Adjustable bimetallic thermostat. To use the bimetallic thermostat as a temperature controller, calculating its hysteresis.
- Adjustable bimetallic thermostat. How we can reduce the hysteresis by adding a resistor to the heating circuit.
- To use the thermostat based on a bimetallic sensor to control the temperature.
- To use the capillary thermostat.
- Using the analog inputs and outputs of the PLC to read and write analog signals.
- Read the temperature sensor signal with the PLC.
- Manual control of the actuator through the PLC.
- PID control of the temperature value through the PLC.
- Observe the effects of the temperature control to changes in the PID parameters.
- Use of linear positioning sensor (potentiometer) to detect the displacement produced by a diaphragm expansion caused by the air pressure.
- Use of a LVDT as an element to measure the diaphragm distortion that is consequence of the pressure inside the pressure chamber.
- Differential pressure sensor with hole-board system. Use of a differential pressure sensor of the semiconductor type to measure the pressure fall in a hole-board system.
- Strain gauges. To detect objects using an infrared sensor by light beam interruption.
- Measure the pressure in the chamber, using two different types of sensors (manometric and absolute pressure sensor).
- Strain gauges for measuring deformations: their resistance changes as the diaphragm expands due to the pressure coming from the pressure chamber.
- Using the analog inputs and outputs of the PLC to read and write analog signals.
- Read the pressure sensor signal with the PLC.
- Manual control of the actuator through the PLC.
- PID control of the pressure value through the PLC.
- Observe the effects of the pressure control to changes in the PID parameters.
- To measure the water volume produced by an underwater pump in the module using an optical flow sensor.
- To use a high-resolution optical flow sensor to measure low flow volumes.
- Pressure level sensor. To use a differential pressure sensor to measure the liquid level in one of the tanks.
- Differential pressure sensor. To measure the pressure-fall in themodule hole board system, as a necessary parameter todetermine volume.
- To measure the flow volume generated by the underwater pumpusing a flow meter of changeable area.
- To obtain the flow-volume value in the secondary tank using the Vnarrowing weir.
- Using the analog inputs and outputs of the PLC to read and write analog signals.
- Read the flow sensor signal with the PLC.
- Manual control of the actuator through the PLC.
- PID control of the flow value through the PLC.
- Observe the effects of the flow control to changes in the PID parameters.
- Heating element. Raise the oven internal temperature, over the environmental temperature, using a heating element to do tests and practices related with temperature measurement.
- To use a fan as refrigerating element of the oven.
- To use thermocouples as temperature sensors elements inside the oven. Temperature measurement using a thermocouple.
- To measure temperature inside the oven using a platinum resistance thermometer.
- To measure temperature inside the oven using a thermistor temperature sensor.
- Temperature measurement using a thermistor, based on its negative temperature coefficient.
- To obtain the temperature value inside the oven using a semiconductor sensor (diode).
- Using the analog inputs and outputs of the PLC to read and write analog signals.
- Read the temperature sensor signal with the PLC.
- Manual control of the actuator through the PLC.
- PID control of the temperature value through the PLC.
- Observe the effects of the temperature control to changes in the PID parameters.
- To use a capacitive sensor to measure the liquid level in the tank.
- To use the differential pressure sensor as an element to determine the water level in a tank.
- To use a changeable resistance fixed to a float system as a liquid level measurement element.
- Conduction Sensor. Use of a sensor made up of to steel electrodes to measure the water level of a tank.
- Magnetic float level sensor. It detects a precise liquid level in the tank with a magnetic contact.
- Control of the module left tank liquid level using an optical level sensor.
- Using the analog inputs and outputs of the PLC to read and write analog signals.
- Read the tachometer signal with the PLC.
- Manual control of the actuator through the PLC.
- PID control of the angular speed value through the PLC.
- Observe the effects of the angular speed control to changes in the PID parameters.
- DC Motor. Provide the group of sensors of the "BS-7" module fixed to the central axle of the equipment with movement power.
- DC Tachometer. To use a DC motor as a tachometer to measure the revolutions of the "BS-7" module central axle.
- Inductive Sensor.
- Retroreflective optical sensor. To measure the central axle revolutions of the module using a light reflection optical sensor.
- To obtain the central axle speed value using a slot optical sensor through light interruption.
- To obtain the central axle speed value using a Hall-effect position sensor.
- To measure the central axle revolutions of the module using the encoder.
- Using the analog inputs and outputs of the PLC to read and write analog signals.
- Read the tachometer signal with the PLC.
- Manual control of the actuator through the PLC.
- PID control of the angular speed value through the PLC.
- Observe the effects of the angular speed control to changes in the PID parameters.
- Proportional valves. To control electronically the vertical displacement of a double effect pneumatic piston using proportional valves.
- Differential pressure sensor. To use a pressure sensor for measuring the pressure difference between both pneumatic piston air inlets.
- Pneumatic switch. To deflect the air flow using a pneumatic switch.
- LVDT Linear Displacement Sensor. To measure pneumatic piston displacement using an excitation and DC output LVDT.
- Using the analogs input and outputs of the PLC to read and write analog signals.
- Read the position sensor signal with the PLC.
- Manual control of the actuator through the PLC.
- PID control of the cylinder position through the PLC.
- Observe the effects of the position control to changes in the PID parameters.
- Study of the equivalent electrical circuit of a photodiode. Study the V-I characteristic of a photodiode.
- Study of the normal operation mode of a photodiode. Study the "ON/OFF" operation (light switch) of a phototransistor.
- Measurement of light intensity using a solar cell.
- Study of the properties of light dependent resistors (LDR).
- Study of the operation of IR sensors.
- Using the analog inputs and outputs of the PLC to read and write analog signals.
- Read the light sensor signal with the PLC.
- Manual control of the actuator through the PLC.
- PID control of the light intensity value through the PLC.
- Observe the effects of the light intensity control to changes in the PID parameters.
補完的な機器
6.2.3.- PLCによる計装と制御
BS2-PLC
PLC用温度試験モジュール
The "BS2-PLC" has been designed to study the use and applications of temperature sensors as a measure device and how to perform a temperature control through a PLC. TThe unit has a half-open space inside which there is a lamp that heats the...
6.2.3.- PLCによる計装と制御
BS3-PLC
PLC用圧力試験モジュール
The "BS3-PLC" has been designed to study the pressure measurement techniques and control application with a PLC. This unit is equipped with a pressure chamber with several sensors, with different uses and applications, adjusted to measure the...
6.2.3.- PLCによる計装と制御
BS4-PLC
PLC用流量試験モジュール
The "BS4-PLC" has been designed to study the flow measurement techniques and control with PLC. This unit is unit with two tanks assembled on a structure with a pumping system that allows pumping the water from the reservoir tank, through the...
6.2.3.- PLCによる計装と制御
BS5-PLC
PLC用炉の試験モジュール
The "BS5-PLC" has been designed to study the temperature measurement techniques inside a sealed place, such as an oven and how to perform a temperature control through a PLC. This unit is equipped with an oven that contains a heating element and a...
6.2.3.- PLCによる計装と制御
BS6-PLC
PLC用液面試験モジュール
The "BS6-PLC" has been designed to study the liquid level measurement and control techniques of a tank through a PLC. This unit is unit with two tanks with sensor of different technology for level measurement. One of the level sensor output...
6.2.3.- PLCによる計装と制御
BS7-PLC
PLC用タコメーター試験モジュール
The "BS7-PLC" has been designed to study the linear and angular speed measurement techniques through a PLC. This unit is unit with a miniature motor to move an axle at different speeds, being able to adjust de motor speed by changing the voltage...
6.2.3.- PLCによる計装と制御
BS9-PLC
PLC用空気圧試験モジュール
The "BS9-PLC" has been designed to study the control and handling techniques of a pneumatic actuator through a PLC. The actuator is a double acting pneumatic cylinder that allows moving a platform. The displacement of the piston axle is detected...
6.2.3.- PLCによる計装と制御
BS10-PLC
PLC用照明試験モジュール
The "BS10-PLC" has been designed to study different light measurement techniques and control light intensity through a PLC. This unit is composed of a lamp whose intensity can be controlled according to the voltage applied and a series of...
品質
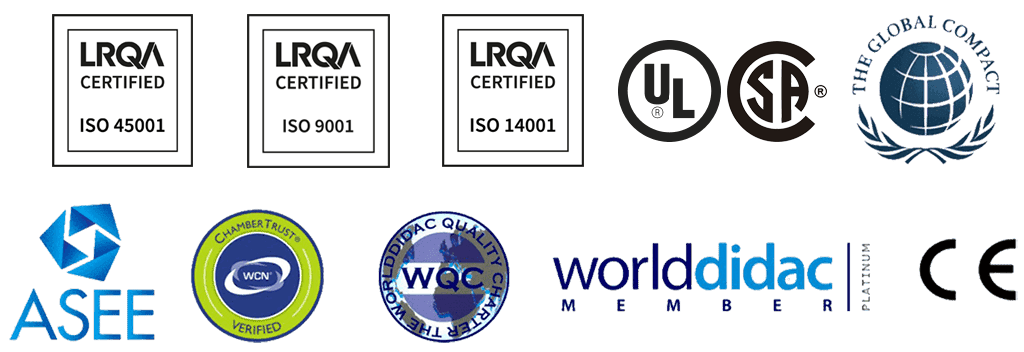
アフターサービス
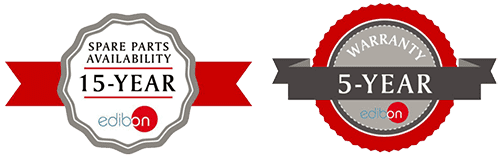