UCP 프로세스 제어 (전자 밸브), 컴퓨터 제어 (PC)
혁신적인 시스템
The Computer Controlled Process Control (Electronic Valve), "UCP", designed by EDIBON, allows the study of several types of automatic control and can be used to control different variables (flow, level, temperature, pressure, pH, conductivity and TDS) in several ways.
실험실
관련 뉴스
일반적인 설명
The Computer Controlled Process Control (Electronic Valve), "UCP", designed by EDIBON, allows the study of several types of automatic control and can be used to control different variables (flow, level, temperature, pressure, pH, conductivity and TDS) in several ways.
The control is done automatically by acting on an electronic valve.
The minimum supply consists of two main elements: the Base Unit for UCP, "UCP-UB", and at least one of the required elements described below.
The main elements of the Base Unit for UCP, "UCP-UB", are:
- Storage tank and collector at the top of the unit with hole in the central dividing wall and drainage in both compartments (methacrylate).
- Dual process tank, interconnected through an orifice and a ball valve and overflow in the dividing wall, preventing the complete flooding of the tank and allowing to modify its effective liquid volume.
- Hydraulic circuit composed by two centrifugal circulation pumps, two flow meters, three all/nothing solenoid valves and a motorized proportional valve (infinitely variable) for control.
- Helix stirrer, which guarantees a good uniformity of the variables to be controlled.
Required elements (at least one) (Not included):
- UCP-T. Set for Temperature Process Control for UCP.
- UCP-C. Set for Flow Process Control for UCP.
- UCP-N. Set for Level Process Control for UCP.
- UCP-PA. Set for Water Pressure Process Control for UCP.
- UCP-PH. Set for pH Process Control for UCP.
- UCP-CT. Set for Conductivity and TDS (Total dissolved Solids) for UCP.
All these required elements, designed by EDIBON, allow the user to perform different types of controls, and to study experimentally the different responses of the system. It will be possible to perform closed loop control by means of an all or nothing controller (ON/OFF), learn how to reach a desired value manually, perform control by means of a proportional controller (P), perform control by means of a proportional + Integral controller (PI), perform control by means of a proportional + Derivative controller (PD), study experimentally the characteristics of the integral, proportional or derivative component of a PID controller, adjust the components of a PID controller for the control of different variables, etc.
In addition, all our units are supplied with a process diagram explaining the location of all elements, valves, sensors, actuators, etc. found in the unit.
This Computer Controlled Unit is supplied with the EDIBON Computer Control System (SCADA), and includes: The unit itself + a Control Interface Box + a Data Acquisition Board + Computer Control, Data Acquisition and Data Management Software Packages, for controlling the process and all parameters involved in the process.
연습 및 가이드
매뉴얼에 포함 된 가이드 실기 연습
Practices to be done with the Set for Temperature Process Control for UCP (UCP-T):
- Temperature control loops (Manual).
- Temperature control loops (On/Off).
- Response of a temperature system to a step input.
- Temperature control loops (Proportional).
- Temperature control loops (Proportional + Integral).
- Temperature control loops (Proportional + Derivative).
- Temperature control loops (Proportional + Derivative + Integral).
- PID tuning for a temperature control system (Ziegler-Nichols).
- Adjustment of the constant of a controller of temperature (Reaction Curves).
- Temperature sensor calibration.
Practices to be done with the Set for Flow Process Control for UCP (UCP-C):
- Flow control loops (Manual).
- Flow control loops (On/Off).
- Response of a flow system to a step input.
- Flow control loops (Proportional).
- Flow control loops (Proportional + Integral).
- Flow control loops (Proportional + Derivative).
- Flow control loops (Proportional + Derivative + Integral).
- PID tuning for a flow control system (Ziegler-Nichols).
- Adjustment of the flow controller constants (Reaction Curves).
- Flow sensor calibration.
Practices to be done with the Set for Level Process Control for UCP (UCP-N):
- Level control loops (Manual).
- Level control loops (On/Off).
- Response of a level system to a step input.
- Level control loops (Proportional).
- Level control loops (Proportional + Integral).
- Level control loops (Proportional + Derivative).
- Level control loops (Proportional + Derivative + Integral).
- PID tuning for a level control system (Ziegler-Nichols).
- Adjustment of the constants of a level controller (Reaction Curves).
- Level sensor calibration.
Practices to be done with the Set for Water Pressure Process Control for UCP (UCP-PA):
- Pressure control loops (Manual).
- Pressure control loops (On/Off).
- Response of a pressure system to a step input.
- Pressure control loops (Proportional).
- Pressure control loops (Proportional + Integral).
- Pressure control loops (Proportional + Derivative).
- Pressure control loops (Proportional + Derivative + Integral).
- PID tuning for a pressure control system (Ziegler-Nichols).
- Adjustment of the constants of a pressure controller (Reaction Curves).
- Pressure sensor calibration.
Practices to be done with the Set for pH Process Control for UCP (UCP-PH):
- pH control loops (Manual).
- pH control loops (On/Off).
- Response of a pH system to a step input.
- pH control loops (Proportional).
- pH control loops (Proportional + Integral).
- pH control loops (Proportional + Derivative).
- pH control loops (Proportional + Derivative + Integral).
- PID tuning for a pH control system (Ziegler-Nichols).
- Adjustment of the constant of a pH controller (Reaction Curves).
- pH sensor calibration.
Practices to be done with the Set for Conductivity and TDS (Total dissolved Solids) for UCP (UCP-CT):
- Conductivity control loops (Manual).
- Conductivity control loops (On/Off).
- Response of a conductivity system to a step input.
- Conductivity control loops (Proportional).
- Conductivity control loops (Proportional + Integral).
- Conductivity control loops (Proportional + Derivative).
- Conductivity control loops (Proportional + Derivative + Integral).
- PID tuning for a conductivity control system (Ziegler-Nichols).
- Adjustment of the constant of a conductivity controller (Reaction Curves).
- TDS control loops (Manual).
- TDS control loops (On/Off).
- Response of a TDS system to a step input.
- TDS control loops (Proportional).
- TDS control loops (Proportional + Integral).
- TDS control loops (Proportional + Derivative).
- TDS control loops (Proportional + Derivative + Integral).
- PID tuning for a TDS control system (Ziegler-Nichols).
- Adjustment of the constant of a TDS controller (Reaction Curves).
- Conductivity and TDS sensor calibration.
Cascade process control:
- Temperature and level cascade control.
- Temperature and flow cascade control.
- Temperature and pressure cascade control.
장비로 수행 할 수있는 더 많은 실용적 연습
- Many students view results simultaneously. To view all results in real time in the classroom by means of a projector or an electronic whiteboard.
- Open Control, Multicontrol and Real Time Control. This unit allows intrinsically and/or extrinsically to change the span, gains, proportional, integral, derivative parameters, etc, in real time.
- The Computer Control System with SCADA and PID Control allow a real industrial simulation.
- This unit is totally safe as uses mechanical, electrical and electronic, and software safety devices.
- This unit can be used for doing applied research.
- This unit can be used for giving training courses to Industries even to other Technical Education Institutions.
- Control of the UCP unit process through the control interface box without the computer.
- Visualization of all the sensors values used in the UCP unit process.
- By using PLC-PI additional 19 more exercises can be done.
- Several other exercises can be done and designed by the user.
비슷한 제품
프로세스 제어 (속도 조절기), 컴퓨터 제어 (PC)
프로세스 제어 (전기 + 공압 밸브 및 인버터), 컴퓨터 제어 (PC)
보완 장비
컴퓨터(PC)로 제어되는 연결 탱크 시스템
프로세스 제어 (공압 밸브), 컴퓨터 제어 (PC)
프로세스 제어 (속도 조절기), 컴퓨터 제어 (PC)
프로세스 제어 (전기 + 공압 밸브 및 인버터), 컴퓨터 제어 (PC)
Computer Controlled Process Control Unit for the Study of Pressure (Air)
산업용 프로세스 제어 시스템, 컴퓨터(PC)에서 제어됨
품질
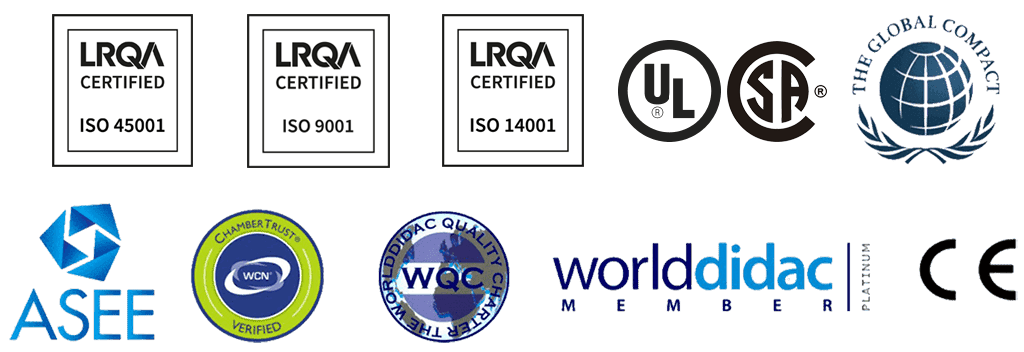
판매 후 서비스
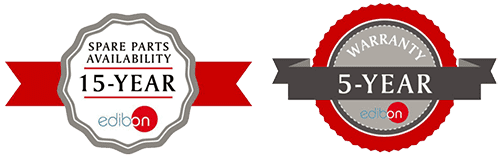