What are Organic Rankine Cycle Applications?
What is?
Internal combustion engines convert only 30% of the fuel energy content into useful mechanical energy, the 70 % remaining energy, at a lower temperature, is wasted through the engine exhaust and cooling systems to the atmosphere.
One of the most promising technologies of Waste Heat to take advantage of this energy is the Organic Rankine Cycle ORC.
The ORC uses an organic gas (pentane,octane, R123, etc.) as the working agent of the cycle because of its low boiling temperature (< 80ºC ),instead that of the Rankine Steam Water Cycle of the thermal power stations.
A typical ORC plant consists of an evaporator, an expansion device and a condenser.
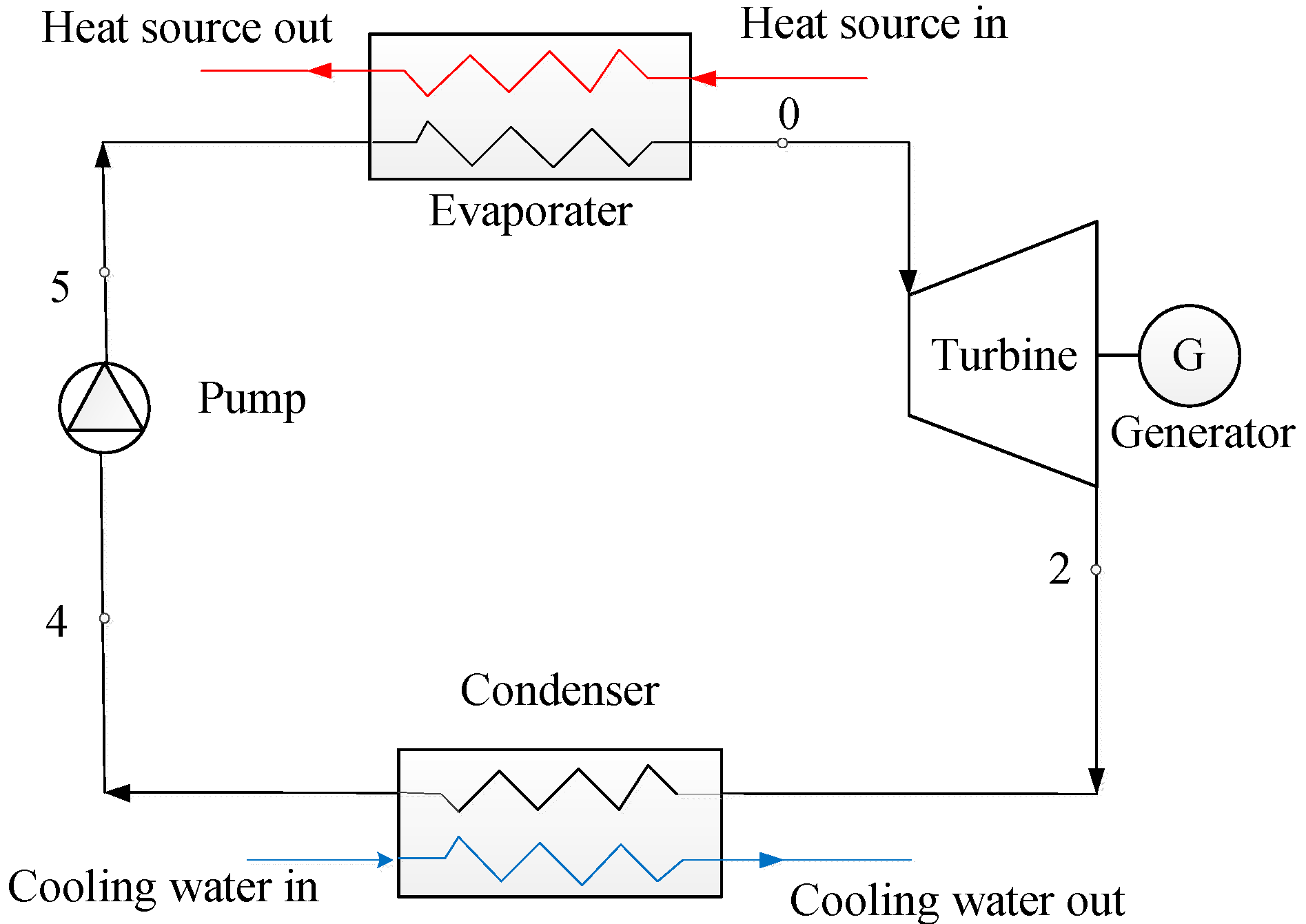
Similarly to a conventional Rankine Cycle, in the ORC the organic gas passes through the evaporator heat exchanger, being heated by the exhaust gases of the internal combustion engine. After that, it enters in an expansion device (such as a turbine, screw, scroll, vane or other type of expander) connected to an electric generator. Then it is cooled and condensed in the condenser heat exchanger.
Thus the ORC (Organic Rankine Cycle) can be used as a bottoming cycle in any industrial application where the gases going out of the process , are at temperatures between 400ºC to 200ºC .In this way it can be avoided to discharge and waste the energy of the exhaust gases into the atmosphere.
The efficiency of the technology is in the range of 20 - 24 % for high temperatures of 400ºC and 8-12 % in the lower range of 150-200 ºC.
As the ORC works only in one phase , there is no need to install a superheater ,therefore simplifying the plant .On the other hand as there are a wide number of working fluids for the cycle, an important issue is to select the best one for the application ,depending on the power of the ORC plant and temperature of the exhaust gases entering on the cycle.
It´s a mature technology with installation costs in the range of 2000-3000 € /KWe for a plant of 50 KWe.
Applications:
The Waste Heat Recovery (WHR ) market is divided in small (< 1 MW ) and large ORCs up to 20 MW and includes industrial sectors like:
Cement factories, electric thermal power plants, steel factories etc where an exhaust energy is lost.
In the field of renewables can be also cited:
- Geothermal power plant: ORC can be applied to the exhaust of Geothermal plants with output temperatures from 100ºC to 400º C. Below 100ºC the efficiency cycle is is too low and therefore is not applicable.
- Biomass power plant: One of the advantages of ORC is the low working pressure which reduces the cost of the equipment compared with conventional ones also that is suitable for smaller power plants.
- Solar thermal plant: In solar power plant with trough collector where the oil working fluid, the ORC can be installed at the end of the plant to increase their efficiency by at least 15%.
In addition to these industrial application the ORC is successfully utilized in small units on the range 1 to 10 KWe at home applications, but with the penalty of a low efficiency 7- 8 %
EDIBON TORC ORGANIC RANKINE CYCLE:
Description:
Computer Controlled Organic Rankine Cycle Unit, “TORC”, allows the student to study the complete process and the components of an organic Rankine Cycle, as well as the main variables that take part in the process.
The working fluid (coolant R-245fa) is evaporated by applying a heat source. First of all, the coolant is impelled by a computer controlled pump through a plate exchanger (preheater) through which the tap water heated in the cycle condenser flows in countercurrent.
Then, the organic working fluid passes through two plate exchangers that constitute the cycle evaporator, through which superheated water to 150 ºC (heat source) flows impelled by a pump. Superheated water is generated in a boiler with a heating element (resistor), which can be controlled through the computer with a PID control, indicating the set-point to which the water wants to be heated.
The boiler has a safety level switch. After the heat is transferred, the superheated water returns to the boiler at the outlet of the second exchanger. There is a purge valve in this close circuit of superheated water, a bypass circuit and purges to remove the air from the circuit. The organic fluid steam is expanded in the turbine when it reaches the working conditions, generating an electrical power which is measured.
At the outlet of the turbine the organic fluid is condensed by means of a water flow in a plate exchanger. The tap water heated in the organic working fluid condensing process is directed to the preheater to take advantage of the waste heat. The condensate is collected in an intermediate tank, with two level actuators.
When the level is enough, the organic fluid is pumped backwards again and the thermodynamic cycle is closed this way. The cooling and heating sources are not directly in contact with the working fluid or the turbine.
This Computer Controlled Unit is supplied with the EDIBON Computer Control System (SCADA), and includes: The unit itself + a Control Interface Box + a Data Acquisition Board + Computer Control, Data Acquisition and Data Management Software Packages, for controlling the process and all parameters involved in the process.