At EDIBON, we are committed to strengthening skills as a strategic pillar for the competitiveness and social well-being of the European Union. Proper training not only boosts the economy but also enables individuals to fully participate in society and democracy.
AE-PLC-FMS7 Sistema de Manufatura Flexível para Alimentação, Identificação, Classificação e Transporte
SISTEMAS INOVADORES
The Flexible Manufacturing System for Feeding, Identification, Classification, and Transport, "AE-PLC-FMS7", designed by EDIBON, enables the study and practice of an automated production cycle consisting of 4 distinct workstations. This system integrates all the mentioned workstations, as well as an additional feeding station.
NOTÍCIAS RELACIONADAS
Descrição Geral
The Flexible Manufacturing System for Feeding, Identification, Classification, and Transport, "AE-PLC-FMS7", is a highly adaptable and configurable system designed for the study and application of advanced automation principles within the context of Industry 4.0 and Industry 5.0. This unit integrates key technologies such as automated control, inter-device networking through smart networks, PLC programming of assembly lines, and real-time data analysis, allowing users to explore the capabilities of digitized and connected manufacturing that characterize the Fourth Industrial Revolution and pave the way for the Fifth Industrial Revolution.
It consists of four interconnected stations that perform specific tasks related to feeding, transport, assembly, sorting (dimension, material, and color), screwing, and parts storage. Each of these workstations requires its own PLC from the selected brand (PANASONIC, SIEMENS, ALLEN BRADLEY, MITSUBISHI and/or OMRON), allowing users to explore how advanced control and production concepts are applied in an automated manufacturing line. The workflow is coordinated by a central PLC system (from the same brand chosen for the stations) and an Ethernet network, making the "AE-PLC-FMS7" a comprehensive learning resource for those interested in automation engineering and flexible manufacturing.
The included workstations are:
- Parts Feeding Workstation, "AE-PLC-A": Starts the cycle by moving base parts with different sizes, colors, and dimensions from the waiting position to the conveyor belt.
- Linear Transport Workstation, "AE-PLC-T": Receives the parts from the storage workstation and positions them for the next workstation.
- Parts Identification Workstation, "AE-PLC-SIP": Detects the characteristics of each part to discard any invalid pieces. Valid pieces are placed back on the Linear Transport Workstation, "AE-PLC-T."
- Sorting Workstation, "AE-PLC-CF", finally, parts with the required color, material, and height patterns are selected based on the code created by the student, while the remaining parts are discarded.
The system allows students and instructors to delve into fundamental concepts of industrial automation. Through its use, students acquire practical skills in designing and operating automated systems, gaining a deep understanding of the coordinated work across the various workstations of a real production line. This configurable system has been carefully designed so that each of its workstations performs specific functions that simulate real industrial processes.
The recommended Automation System Simulation Software, "AE-AS," enables the simulation of industrial processes in both 2D and 3D, providing full control and supervision, allowing users to safely experiment with automation software in a protected environment.
EXERCÍCIOS E PRÁTICAS GUIADAS
EXERCÍCIOS PRÁTICOS GUIADOS INCLUÍDOS NO MANUAL
Practical possibilities to be done with the Flexible Manufacturing System for Feeding, Identification, Classification, and Transport (AEPLC-FMS7):
- Introduction to flexible manufacturing system (FMS).
- Introduction to pneumatics and electro-pneumatics.
- Introduction to vacuum technology.
- Study of the sensor detection.
- Testing the digital inputs and outputs of the automatic system through a PLC.
- Modify manufacturing parameters through the PLC.
- Configuration of a pneumatic application.
- Introduction to the Human-machine interface systems (HMI).
- Study of an automatic control of an industrial system.
- Control of the flexible manufacturing system through a central PLC in an Ethernet network with local PLC in each workstation.
- Manage the flexible manufacturing system through the HMI device.
Practical possibilities to be done with the workstation alone:- Feeding Workstation for Pieces (AE-PLC-A).
- Manual control of a Feeding system.
- Automatic control of a Feeding system.
- Change the parameters of the Feeding process.
- Optimize the process time.
- Study and analysis of the faults inserted in the process with the fault generation module.
- Linear Transport Workstation (AE-PLC-T).
- Manual control of a transporting system.
- Automatic control of a transporting system.
- Change the parameters of a transporting process.
- Optimize the process time.
- Study and analysis of the faults inserted in the process with the fault generation module.
- Pieces Identification Workstation (AE-PLC-SIP).
- Manual control of a quality control system.
- Automatic control of a quality control system.
- Change the parameters of the quality control system.
- Optimize the process time.
- Study and analysis of the faults inserted in the process with the fault generation module.
- Sorting Workstation (AE-PLC-CF).
- Manual control of a sorting system.
- Automatic control of a sorting system.
- Change the parameters of the sorting process.
- Optimize the process time.
- Study and analysis of the faults inserted in the process with the fault generation module.
Practical possibilities to be done with the optional software Automation Systems Simulation Software (AE-AS):
- Introduction to the SCADA control system.
- OPC server system with Ethernet.
- SCADA control of an automatic industrial system through PC.
EQUIPAMENTOS SIMILARES DISPONÍVEIS
6.2.6.- SISTEMAS FLEXÍVEIS DE FABRICAÇÃO COM PLC
AE-PLC-FMS2
The Flexible Manufacturing System for Transport, Assembly, Selection, Screwing, and Storage, "AE-PLC-FMS2", is a highly adaptable and configurable system designed for the study and application of advanced automation principles within the context...
6.2.6.- SISTEMAS FLEXÍVEIS DE FABRICAÇÃO COM PLC
AE-PLC-FMS3
Sistema de Manufatura Flexível para Transporte, Montagem, Seleção (Material e Cor) e Armazenamento
The Flexible Manufacturing System for Transport, Assembly, Selection (Material and Color), and Storage, "AE-PLC-FMS3", is a highly adaptable and configurable system designed for the study and application of advanced automation principles within...
6.2.6.- SISTEMAS FLEXÍVEIS DE FABRICAÇÃO COM PLC
AE-PLC-FMS4
Sistema de Manufatura Flexível para Filtragem, Mistura, Controle de Processos Industriais e Envase
The Flexible Manufacturing System for Filtering, Mixing, Industrial Process Control, and Bottling, "AE-PLC-FMS4", is a highly adaptable and configurable system designed for the study and application of advanced automation principles within the...
6.2.6.- SISTEMAS FLEXÍVEIS DE FABRICAÇÃO COM PLC
AE-PLC-FMS5
Sistema de Manufatura Flexível para Transporte, Classificação, Seleção e Manipulação Pneumática
Flexible Manufacturing System for Transport, Classification, Selection, and Pneumatic Handling, "AE-PLC-FMS5," is a highly adaptable and configurable system designed for the study and application of advanced automation principles within the...
6.2.6.- SISTEMAS FLEXÍVEIS DE FABRICAÇÃO COM PLC
AE-PLC-FMS6
Sistema de Manufatura Flexível para Alimentação e Classificação
The Flexible Manufacturing System for Feeding and Classification, "AE-PLC-FMS6", is a highly adaptable and configurable system designed for the study and application of advanced automation principles within the context of Industry 4.0 and Industry...
6.2.6.- SISTEMAS FLEXÍVEIS DE FABRICAÇÃO COM PLC
AE-PLC-FMS1
Sistema de Manufatura Flexível para Transporte, Montagem, Prensagem, Seleção, Parafusamento e Armazenamento
The Flexible Manufacturing System for Transport, Assembly, Pressing, Selection, Screwing, and Storage, "AE-PLC-FMS1", is a highly adaptable and configurable system designed for the study and application of advanced automation principles within the...
6.2.6.- SISTEMAS FLEXÍVEIS DE FABRICAÇÃO COM PLC
AE-PLC-FMS14
Sistema de Manufatura Flexível para Controle de Processos Industriais, Enchimento, Selagem e Armazenamento
The Flexible Manufacturing System for Industrial Process Control, Filling, Sealing, and Storage, "AE-PLC-FMS14", is a highly adaptable and configurable system designed for the study and application of advanced automation principles within the...
6.2.6.- SISTEMAS FLEXÍVEIS DE FABRICAÇÃO COM PLC
AE-PLC-FMS15
Sistema de Manufatura Flexível para Alimentação, Montagem, Manipulação Robótica e Transporte
The Flexible Manufacturing System for Feeding, Assembly, Robotic Handling, and Transport, "AE-PLC-FMS15", is a highly adaptable and configurable system designed for the study and application of advanced automation principles within the context of...
EQUIPAMENTOS COMPLEMENTARES
6.2.6.- SISTEMAS FLEXÍVEIS DE FABRICAÇÃO COM PLC
AE-PLC-FMS1
Sistema de Manufatura Flexível para Transporte, Montagem, Prensagem, Seleção, Parafusamento e Armazenamento
The Flexible Manufacturing System for Transport, Assembly, Pressing, Selection, Screwing, and Storage, "AE-PLC-FMS1", is a highly adaptable and configurable system designed for the study and application of advanced automation principles within the...
6.2.6.- SISTEMAS FLEXÍVEIS DE FABRICAÇÃO COM PLC
AE-PLC-FMS2
Sistema de Manufatura Flexível para Transporte, Montagem, Seleção, Parafusamento e Armazenamento
The Flexible Manufacturing System for Transport, Assembly, Selection, Screwing, and Storage, "AE-PLC-FMS2", is a highly adaptable and configurable system designed for the study and application of advanced automation principles within the context...
6.2.6.- SISTEMAS FLEXÍVEIS DE FABRICAÇÃO COM PLC
AE-PLC-FMS3
Sistema de Manufatura Flexível para Transporte, Montagem, Seleção (Material e Cor) e Armazenamento
The Flexible Manufacturing System for Transport, Assembly, Selection (Material and Color), and Storage, "AE-PLC-FMS3", is a highly adaptable and configurable system designed for the study and application of advanced automation principles within...
6.2.6.- SISTEMAS FLEXÍVEIS DE FABRICAÇÃO COM PLC
AE-PLC-FMS4
Sistema de Manufatura Flexível para Filtragem, Mistura, Controle de Processos Industriais e Envase
The Flexible Manufacturing System for Filtering, Mixing, Industrial Process Control, and Bottling, "AE-PLC-FMS4", is a highly adaptable and configurable system designed for the study and application of advanced automation principles within the...
6.2.6.- SISTEMAS FLEXÍVEIS DE FABRICAÇÃO COM PLC
AE-PLC-FMS5
Sistema de Manufatura Flexível para Transporte, Classificação, Seleção e Manipulação Pneumática
Flexible Manufacturing System for Transport, Classification, Selection, and Pneumatic Handling, "AE-PLC-FMS5," is a highly adaptable and configurable system designed for the study and application of advanced automation principles within the...
6.2.6.- SISTEMAS FLEXÍVEIS DE FABRICAÇÃO COM PLC
AE-PLC-FMS6
Sistema de Manufatura Flexível para Alimentação e Classificação
The Flexible Manufacturing System for Feeding and Classification, "AE-PLC-FMS6", is a highly adaptable and configurable system designed for the study and application of advanced automation principles within the context of Industry 4.0 and Industry...
6.2.6.- SISTEMAS FLEXÍVEIS DE FABRICAÇÃO COM PLC
AE-PLC-FMS14
Sistema de Manufatura Flexível para Controle de Processos Industriais, Enchimento, Selagem e Armazenamento
The Flexible Manufacturing System for Industrial Process Control, Filling, Sealing, and Storage, "AE-PLC-FMS14", is a highly adaptable and configurable system designed for the study and application of advanced automation principles within the...
6.2.6.- SISTEMAS FLEXÍVEIS DE FABRICAÇÃO COM PLC
AE-PLC-FMS15
Sistema de Manufatura Flexível para Alimentação, Montagem, Manipulação Robótica e Transporte
The Flexible Manufacturing System for Feeding, Assembly, Robotic Handling, and Transport, "AE-PLC-FMS15", is a highly adaptable and configurable system designed for the study and application of advanced automation principles within the context of...
Qualidade
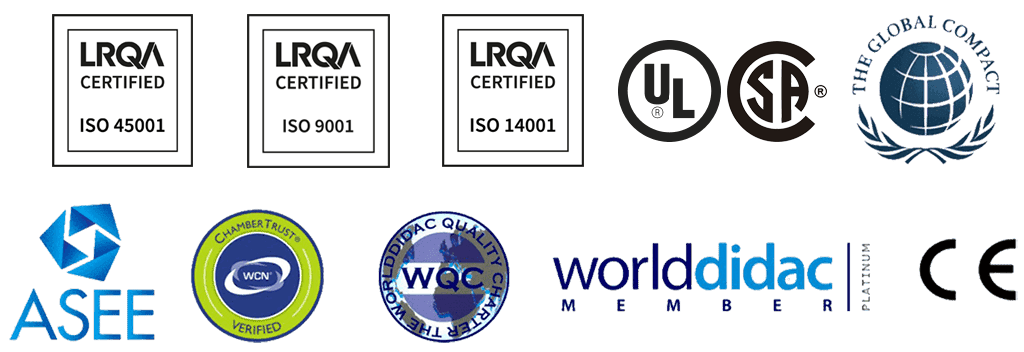
Serviço pós-venda
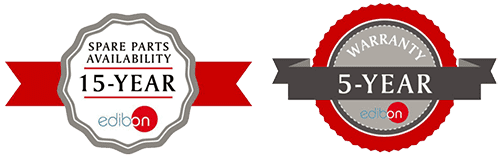