QRQC Обучающая система по работе с химическими реакторами, программируемая с ПК
ИННОВАЦИОННЫЕ СИСТЕМЫ
The Computer Controlled Chemical Reactors Training System, "QRQC," has been designed by EDIBON to facilitate advanced study for students, professors and researchers on the attributes, scenarios, and various types of reactors prevalent in the chemical industry.
ЛАБОРАТОРИИ
НОВОСТИ ПО ТЕМЕ
ОБЩЕЕ ОПИСАНИЕ
The Computer Controlled Chemical Reactors Training System, "QRQC," has been designed by EDIBON to facilitate advanced study for students, professors and researchers on the attributes, scenarios, and various types of reactors prevalent in the chemical industry.
These reactors enable the analysis of residence time, reaction temperature and the presence of inert gases in reactors with volumes of up to 2 liters. The scope of supply for these reactors includes a temperature control system (up to 70 °C), three 10-liter tanks, reagent feeding pumps (up to 7 l/min), and a flow control system for gas-phase products (up to 1440 Nl/h), thus allowing for a comprehensive study of the characteristics or scenarios that may occur in different types of reactors.
The Base Service Unit, "QRUBI", provides the necessary elements for the operation of the different reactor modules.
It performs the following functions:
- Liquid reagent feeding: comprised of two 10-liter glass tanks, two dosing pumps with a capacity of up to 7 liters per hour, and all necessary connections.
- Gas feeding: consisting of a flow meter, manual regulation valve, and all necessary connections. This allows for the addition of gaseous reagents to the reactor or the introduction of an inert gas.
- Temperature control: comprising a thermostatic bath and a circulation pump.
- Product collection system: Enables the quick and easy transfer of products obtained in the reactors to the base module and their deposition in a 10-liter glass tank.
- Reaction monitoring system: consists of a conductivity cell and a conductivity meter installed on the front panel of the base module.
- This unit allows for reagent feeding, product collection, and temperature control in reactors with a volume of up to 2 liters or more.
These Computer Controlled Units are supplied with EDIBON Computer Control System (SCADA), and includes: The unit itself + a Control Interface Box + a Data Acquisition Board + Computer Control, Data Acquisition and Data Management Software Packages, for controlling the process and all parameters involved in the process.
Аксессуары
Изотермический реактор со смесителем
Изотермический реактор со смесителем и дистилляцией
Трубчатый проточный реактор
Адиабатический изотермический реактор
Реакторы со смесителем, подключенные последовательно
УПРАЖНЕНИЯ И ПРИМЕРЫ С ИНСТРУКЦИЯМИ
РУКОВОДСТВО ПО ПРАКТИЧЕСКИМ УПРАЖНЕНИЯМ ВКЛЮЧЕНО В РУКОВОДСТВО ПОЛЬЗОВАТЕЛЯ
Practices to be done with the Isothermal Reactor with Stirrer (QRIA):
- Determining the ionic conductivities.
- Batch operation. Obtaining the reaction order with respect to the ethyl acetate. Method of initial rates.
- Batch operation. Obtaining the reaction order with respect to the sodium hydroxide. Method of initial rates.
- Batch operation. Calculation of the rate constant. Constant sodium hydroxide initial concentration.
- Batch operation. Calculation of the rate constant. Constant ethyl acetate initial concentration.
- Rate equation formulation.
- Batch operation. Variation of the kinetic constant with temperature. Arrhenius equation.
- Batch operation. Theoretical and experimental conversion comparison. Deviation from ideality.
- Batch operation. Mixture effects.
- Continuous operation.
- Continuous operation. Mixture effects.
- Sensors calibration.
Practices to be done with Isothermal Reactor with Distillation (QRIA/D):
- Determination of the ionic conductivities.
- Batch operation. Obtaining the reaction order with respect to the ethyl acetate. Method of initial rates.
- Batch operation. Obtaining the reaction order with respect to the sodium hydroxide. Method of initial rates.
- Batch operation. Calculation of the rate constant. Constant sodium hydroxide initial concentration.
- Batch operation. Calculation of the rate constant. Constant ethyl acetate initial concentration.
- Rate equation formulation.
- Batch operation. Variation of the kinetic constant with temperature. Arrhenius equation.
- Batch operation. Theoretical and experimental conversion comparison. Deviation from ideality.
- Batch operation. Mixture effects.
- Continuous operation.
- Continuous operation. Mixture effects.
- Sensors calibration.
Practices to be done with the Tubular Flow Reactor (QRFT):
- Determination of the ionic conductivities.
- Theoretical conversion of the tubular reactor.
- Experimental determination of the tubular reactor conversion.
- Dependence on the residence time.
- Determination of the reaction order.
- Dependence of the rate constant and the conversion with the temperature.
- Sensors calibration.
Practices to be done with the Reactors with Stirrer in Series (QRSA):
- Determination of the ionic conductivities.
- Continuous operation with only one reactor.
- Continuous operation with only one reactor with mixture effects.
- Continuous operation with the three reactors.
- Sensors calibration.
Practices to be done with the Adiabatic and Isothermal Reactor (QRAD):
- Determination of the ionic conductivities.
- Batch operation. Obtaining the reaction order with respect to the ethyl acetate. Method of initial rates.
- Bach operation. Obtaining the reaction order with respect to the sodium hydroxide. Method of initial rates.
- Batch operation. Calculation of the rate constant. Constant sodium hydroxide initial concentration.
- Batch operation. Calculation of the rate constant. Constant ethyl acetate initial concentration.
- Rate equation formulation.
- Batch operation. Variation of the kinetic constant with temperature. Arrhenius equation.
- Batch operation. Theoretical and experimental conversion comparison. Deviation from ideality.
- Batch operation. Effect of concentration on conversion.
- Calculation of the heat transfer coefficient of the coil.
- Batch operation. Mixing effects.
- Continuous operation.
- Sensors calibration.
БОЛЬШЕ ПРАКТИЧЕСКИХ УПРАЖНЕНИЙ ДЛЯ РАБОТЫ С УСТРОЙСТВОМ
- Many students view results simultaneously. To view all results in real time in the classroom by means of a projector or an electronic whiteboard.
- Open Control, Multicontrol and Real Time Control. This unit allows intrinsically and/or extrinsically to change the span, gains, proportional, integral, derivate parameters, etc, in real time.
- The Computer Control System with SCADA and PID Control allow a real industrial simulation.
- This unit is totally safe as uses mechanical, electrical and electronic, and software safety devices.
- This unit can be used for doing applied research.
- This unit can be used for giving training courses to Industries even to other Technical Education Institutions.
- Control of the unit process through the control interface box without the computer.
- Visualization of all the sensors values used in the unit process.
- By using PLC-PI additional 19 more exercises can be done.
- Several other exercises can be done and designed by the user.
АНАЛОГИ ОБОРУДОВАНИЯ В НАЛИЧИИ
Химические реакторы, управляемые компьютером (ПК)
Химические реакторы
ДОПОЛНИТЕЛЬНОЕ ОБОРУДОВАНИЕ
Базовое сервисное оборудование
Изотермический реактор со смесителем
Изотермический реактор со смесителем и дистилляцией
Трубчатый проточный реактор
Реакторы со смесителем, подключенные последовательно
Адиабатический изотермический реактор
Химические реакторы, управляемые компьютером (ПК)
Базовая и сервисная единица для QRC
Непрерывный реактор с перемешивающимся резервуаром для QRC
Управляемый компьютером трубчатый проточный реактор для QRC
прерывистый реактор с компьютерным управлением (ПК) для QRC
Реакторы серии с перемешиванием для QRC, с компьютерным управлением (ПК)
КАЧЕСТВО
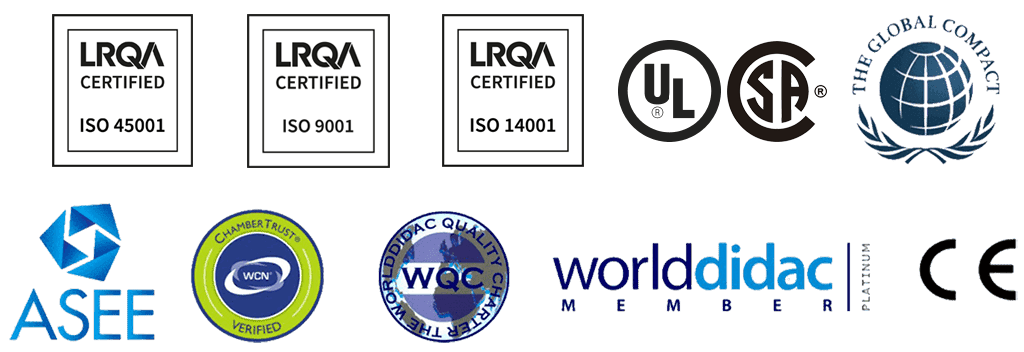
ПОСЛЕПРОДАЖНОЕ ОБСЛУЖИВАНИЕ
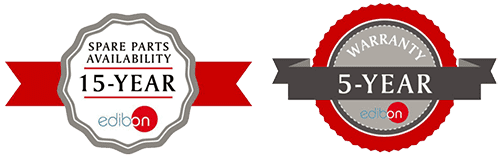