CEAC Оборудование для настройки контроллеров, управляемое с компьютера (ПК)
ИННОВАЦИОННЫЕ СИСТЕМЫ
The Computer Controlled Controller Tuning Unit, "CEAC", provides the tools to simulate different industrial processes in a HIL system and control them with a commercial industrial controller. The CEAC unit works in conjunction with a computer, in order to visualize all signals involved in the process and adjust the parameters of the industrial controller.
ЛАБОРАТОРИИ
НОВОСТИ ПО ТЕМЕ
ОБЩЕЕ ОПИСАНИЕ
The Computer Controlled Controller Tuning Unit, "CEAC", provides the tools to simulate different industrial processes in a HIL system and control them with a commercial industrial controller. The CEAC unit works in conjunction with a computer, in order to visualize all signals involved in the process and adjust the parameters of the industrial controller.The CEAC unit is provided with a set of practical exercises, through which the students will familiarize with the control of most common type of industrial processes, and how to control them with a commercial industrial controller with the following controls: PID (proportional integrative derivative) pPI (predictive proportional integrative), gain scheduling PID for non-linear systems, etc.
The CEAC unit is an advanced system that operates in conjunction with a computer, which allows to change the control parameters performed by the industrial controller.Through the CEAC unit the students will understand the operation mode of an industrial controller. They will learn how to set up thecontroller to control different systems, such as 1st and 2nd order system, time-delayed system, systems with non-linear actuators, etc. andhow to control them using different types of controls such as PID, pPI, gain scheduling, etc. The CEAC unit main components are: the industrial controller and the System Simulator. Both components have an USB connector tocommunicate easily with the computer.In the following lines there is a brief description of each block:
- Industrial Controller: the controller uses one analog input and one analog output, that is enough to perform the control of the singleinput-single output (SISO) systems.The analog input is used to connect the process variable signal (PV). The analog output is used for the output controller signal (O/P).Once the control is configured, the control parameters can be change through the software.
- Process Simulator: performs a real-time hardware-in-the-loop (HIL) simulation of different industrial process, in order to controleach one with the industrial controller. The process simulator can be configured, with the type of the process to simulate (integratorsystem, first order system, second order system, etc.) and the parameters of the system. The simulated system takes the O/P signal fromthe industrial controller and provides the feedback of the system (PV) to the controller.
This Computer Controlled Unit is supplied with the EDIBON Computer Control System (SCADA), and includes: The unit itself + ControlInterface Box + Computer Control, Data Acquisition and Data Management Software Packages, for controlling the process and allparameters involved in the process.
УПРАЖНЕНИЯ И ПРИМЕРЫ С ИНСТРУКЦИЯМИ
РУКОВОДСТВО ПО ПРАКТИЧЕСКИМ УПРАЖНЕНИЯМ ВКЛЮЧЕНО В РУКОВОДСТВО ПОЛЬЗОВАТЕЛЯ
- Familiarization with the navigation of an industrial controller.
- To determine the system parameters in a level control system with a tank without drain (integer system).
- To determine the system parameters in a level control system with a tank with drain (first order system).
- To determine the system parameters in a level control system with two tanks (second order system).
- Study the difference between open and closed loop control.
- Integer system response in open loop.
- Closed loop PID control of an integer system with an industrial controller.
- First order system response in open loop.
- Closed loop PID control of a first order system with an industrial controller.
- Second order system response in open loop.
- Closed loop PID control of a second system with an industrial controller.
- Control of a system with time-delayed response with a predictive proportional integrative (pPI) controller.
- Auto-tuning: Obtaining the PID parameters automatically.
- Control of a system with a non-linear actuator using the gain scheduling controller.
- Alarms and diagnostics generation.
БОЛЬШЕ ПРАКТИЧЕСКИХ УПРАЖНЕНИЙ ДЛЯ РАБОТЫ С УСТРОЙСТВОМ
- Many students view results simultaneously.To view all results in real time in the classroom by means of a projector or an electronic whiteboard.
- Open Control, Multicontrol and Real Time Control. This unit allows intrinsically and/or extrinsically to change the gains, proportional, integral, derivate parameters, etc, in real time.
- The Computer Control System with SCADA allows a real industrial simulation.
- This unit is totally safe as uses mechanical, electrical and electronic, and software safety devices.
- This unit can be used for doing applied research.
- This unit can be used for giving training courses to Industries even to other Technical Education Institutions.
- Several other exercises can be done and designed by the user.
АНАЛОГИ ОБОРУДОВАНИЯ В НАЛИЧИИ
Cеть промышленных контроллеров
Оборудование для применений с полевой шиной
ДОПОЛНИТЕЛЬНОЕ ОБОРУДОВАНИЕ
Оборудование для промышленных контроллеров
Cеть промышленных контроллеров
Оборудование для применений с полевой шиной
КАЧЕСТВО
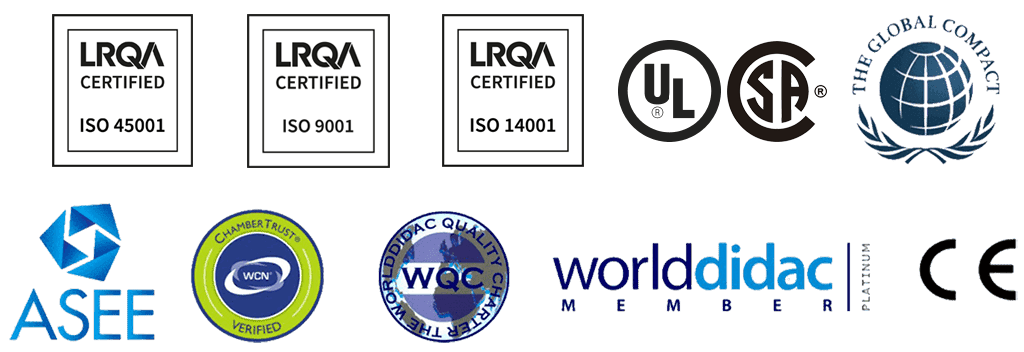
ПОСЛЕПРОДАЖНОЕ ОБСЛУЖИВАНИЕ
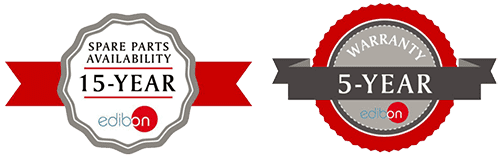