At EDIBON, we are committed to strengthening skills as a strategic pillar for the competitiveness and social well-being of the European Union. Proper training not only boosts the economy but also enables individuals to fully participate in society and democracy.
MDU Диагностика машин
ИННОВАЦИОННЫЕ СИСТЕМЫ
The family of Machine Diagnosis Unit, "MDU", of EDIBON, allows you to perform vibration measurement practical exercises, measuring the displacement, velocity and acceleration of vibrations in the time-frequency range.
НОВОСТИ ПО ТЕМЕ
ОБЩЕЕ ОПИСАНИЕ
The family of Machine Diagnosis Unit, "MDU", of EDIBON, allows you to perform vibration measurement practical exercises, measuring the displacement, velocity and acceleration of vibrations in the time-frequency range.
The MDU Base Unit, "MDU-UB", components are mechanical elements such as: flexible couplings for compensating misalignments, bearings with easily removable roller bearings, two rotor shafts of different lengths, two flywheels with replaceable counterweights and an asynchronous drive motor connected to a frequency converter and a tachometer generator.
All the elements can be mounted on an aluminum frame of 1100 x 770 mm with longitudinal grooves for displacement. They can be easily adjusted using screws.
The unit electronic console makes it possible to show on digital displays the speed and power of the motor, to adjust the motor speed using a potentiometer, and to select the direction of rotation of the motor.
The drive motor is mounted on a sliding carriage that includes two micrometer for precise alignment.
Specific cases of machine faults may be studied with the additional recommended elements, such as: shaft bending vibrations, shaft fissures, roller bearing faults, coupling vibrations, belt drive vibrations, gear faults, pump cavitation, blower vibration, and electromechanical vibrations. Furthermore, with the Bread and Load Unit, "MDU-BLU", ranges of two loading moments may be generated as well as two speed ranges.
The Software, Sensors and Control for MDU Unit, "MDU-SSC" is required to perform all measurements and analyze vibrations.
The MDU Base Unit, "MDU-UB", requires the following to be assembled:
- Mobile Structure for MDU, "MDU-MLB", or
- Top Table Structure for MDU, "MDU-SM".
We also offer the Computer Controlled Machine Diagnosis Unit, "MDUC", which includes the following components:
- MDU Base Unit, "MDU-UB".
- Software, Sensors and Control for MDU Unit, "MDU-SSC".
- Displacement Sensors for MDU Unit, "MDU-SD".
Required elements (Not included):
- MDU-SSC. Software, Sensors and Control for MDU Unit:
- The aim of the vibration analyzer is to assess the machine diagnosis testing with the different kits related to the vibration interface technology.
- The system consists of two acceleration sensors, a speed sensor, a measuring amplifier with adjustable amplification degree, a USB box and the analysis software.
- The analysis software has the following features: two-channel oscilloscope (studies in the time domain), two-channel spectrum analyzer (studies in the frequency domain), vibration intensity gauge, analysis of shock effects and damage in roller bearings, filter for acceleration curve recording, orbit representation and module for single or dual plane balancing of rigid rotors in operation.
- Thanks to the software, it is possible to compare the effectiveness of vibration signals by applying various analysis methods and by determining the advantages and disadvantages of different techniques. Each connection unit includes a 1x, 10x, 100x amplifier, with 16 analog input channels, 4 analog output channels, 4 digital input channels and 4 output channels, which will make possible the coupling of the sensors.
- The optional connection of the additional recommended element, the Displacement Sensors for MDU Unit, "MDU-SD".
- This unit is connected via USB.
- It can be used both in a laptop or a computer.
- Motor control (MDU-UB) and brake control (MDU-BLU) are optional.
Required elements (only one) (Not included):
- MDU-MLB. Mobile Structure for MDU:
- The Mobile Structure for MDU, "MDU-MLB", is a robust structure designed to quickly and easily assemble the various elements of the MDU Base Unit, "MDU-UB" or the Computer Controlled Machine Diagnosis Unit, "MDUC", and thus assemble a mobile test bench for machine diagnosis.
- This structure consists of a slotted table with anodized aluminum frames of 1100 x 770 x 820 mm.
- It has three levels, where the two shelves at the bottom can be used to support the electronic unit and other accessories.
- It also has four steering wheels for easy movement, with brakes on two of them and a transparent protective cover that protects against the rotating parts and allows us to observe the different experiments. The cover includes a safety switch for automatic stop if opened.
- Mobile Structure for MDU, "MDU – MLB" includes:
- MDU-SM. Top Table Structure for MDU.
- TF-WLB. Wheeled Laboratory Bench.
- MDU-SM. Top Table Structure for MDU:
- A bench-top structure consisting of a slotted table with anodized aluminum frames of 1100 x 770 x 820 mm.
- It has a transparent protective cover that protects against the rotating parts and allows us to observe the different experiments. The cover includes a safety switch for automatic stop if opened.
Additional recommended elements (Not included):
- MDU-BLU. Break and Load Unit:
- The Break and Load Unit, "MDU-BLU", of EDIBON is a magnetic particle brake, a display unit and an electrical control. It is possible to precisely adjust the braking moment. The excitation current is used as a measurement of the braking moment and it can be displayed through a console.
- The braking unit consists of an integrated drive belt and a second projecting shaft, thus it has two speed ranges and two moment ranges.
- The power generated is converted into heat by the brake and evacuated to the outside through a fan.
- MDU-SES. Set of Elastic Shaft:
- The Set of Elastic Shaft, "MDU-SES", of EDIBON allows to study the behavior of an elastic rotor subjected to imbalance and balance of elastic rotors in operation. It is possible to study the resonance and the phenomena occurred in subcritical and supercritical regimes with the Displacement Sensors for MDU Unit, "MDU-SD".
- The Set of Elastic Shaft, "MDU-SES", includes some oscillating ball bearings that guarantee the total shaft movement, and the protective bearings limit the amplitude in areas close to the resonance to non-hazardous values.
- MDU-SRS. Set of Rotating Shaft with Crank:
- It is important that fissures resulting from material fatigue in rotating machines are detected in good time before the breakage occurs, which usually leads to fatal consequences.
- The Set of Rotating Shaft with Crank, "MDU-SRS", consists of two shafts with different lengths, the short shaft simulates a projecting shaft end and the load is transmitted with the belt drive of the Set of Belt Drive, "MDU-SBD", whereas the long shaft is used with a protective bearing of the Set of Elastic Shafts, "MDU-SES", and a flywheel in order to study a shaft fissure in the case of an elastic rotor.
- With the Set of Rotating Shaft with Crank, "MDU-SRS", a fissure with very close to real behaviors is simulated. By clamping the flange joint tightly with different forces, small temporary openings in the joint are achieved.
- MDU-SRBF. Set of Roller Bearings with Faults:
- To determine the remaining life cycle of a roller bearing and decide on its replacement, the slow variation of the vibration spectrum is analyzed. The spectral distribution will enable to draw accurate conclusions about the type of defect and its location.
- The Set of Roller Bearings with Faults, "MDU-SRBF", has six roller bearings with which to check and explain several faults in roller bearings, such as: damaged outer ring, damaged inner fault, damaged rolling element, combined damage, very used and new and non-faulty.
- The radial bearing load may be adjusted within certain limits through the Set of Belt Drive, "MDU-SBD".
- MDU-SCO. Set of Couplings:
- The Set of Couplings, "MDU-SCO", allows to compare the properties of different couplings such as curved tooth, bolt, flange and claw couplings.
- The vibrational behavior of the different types of couplings is important to draw conclusions about faults or defects in the manufacturing or assembly of rotating machines. The usual faults are eccentricity, oscillation and pitch errors.
- The Set of Couplings, "MDU-SCO", consists of different couplings to make shaft connections, allowing the study of different types of couplings, faulty and non-faulty.
- MDU-SBD. Set of Belt Drive:
- The belt drives are noiseless drive devices, have a long life and require little maintenance provided that its design, assembly and adjustment are correct. The Set of Belt Drive, "SBD", allows to study the conditions that cause vibrations or slip in belts.
- The set consists of three belts, three pulleys and a set of tensioning rollers and a belt pre-tension meter.
- MDU-SSDG. Set to Study Damage in Gears:
- The Set to Study Damage in Gears, "MDU-SSDG", allows to study the vibrational behavior of gears with typical defects. For that purpose, gears with tooth defects and gears without defects are included, so a comparative study can be carried out. The gears included in the set are helical and straight-toothed gears. Due to the importance of lubrication in the vibrational signal of the unit, this may be lubricated with grease and gear oil.
- The system allows to vary the gear distance and clearance between the teeth.
- MDU-SCM. Set of Crank Mechanism:
- The compressors and pumps frequently use crank and connecting rod mechanisms. The force and mass oscillations cause vibrations in the units.
- The Set of Crank Mechanism, "MDU-SCM", allows to adjust the stroke, mass compensation and bearing clearance, as well as the speed, to simulate vibrations.
- The load is exerted by springs.
- When you want to simulate the force obtained by a gas compression, a higher torque is required, for which it is recommended to use the Set of Belt Drive, "MDU-SBD", or the Set to Study Damage in Gears, "MDU-SSDG".
- MDU-SSCP. Set to Study Cavitation in Pumps:
- Pump cavitation is produced when steam cavities are created within a fluid in which forces act responding to the pressure differences.
- Cavitation causes noise, damage to components and loss of performance.
- The Set to Study Cavitation in Pumps, "MDU-SSCP", allows to produce the cavitation phenomenon and study its vibrational response.
- The Set to Study Cavitation in Pumps, "MDU-SSCP", consists of a single-stage centrifugal pump connected to flexible tubes with a tank. It is possible to adjust different operating conditions with valves and manometers. Furthermore, it is possible to observe the inside of a pump in operation through the plastic casing.
- The pump can be driven directly through an elastic coupling or the Set of Belt Drive, "MDU-SBD".
- MDU-SSVF. Blower Vibration Set for MDU:
- In the Blower Vibration Set for MDU, "MDU-SSVF", the vibrations are magnetically induced. It is possible to study three impellers with a different number of movable vanes. It is also possible to study the gyroscopic effect by mounting the flywheel plate at an oblique angle. A regular fault in the rotation of the roller is induced by the action of a magnet.
- The blower can be driven directly through an elastic coupling or the Set of Belt Drive, "MDU-SBD".
- MDU-SEV. Set of Electromechanical Vibrations:
- Among the drive systems are the asynchronous motors, which generate vibrations in machines.
- This is the case with an asymmetric air gap (space between rotor and stator), in which the magnetic vibrational forces induce torsional and bending vibrations.
- In the event of a partial failure of the electrical windings, mechanical vibrations are produced in the asymmetrical magnetic field.
- The Set of Electromechanical Vibrations, "MDU-SEV", is an adjustable unit that allows to adjust an asymmetric air gap or to disconnect a winding, generating an electromagnetic asymmetry and thus it is possible to study its vibrational behavior.
- MDU-SD. Displacement Sensors for MDU Unit:
- Two displacement sensors which, together with the Set of Elastic Shaft ,"MDU-SES", and the Software, Sensors and Control for MDU Unit, "MDU-SSC", allow you to represent subcritical and supercritical shaft orbits in resonance.
Аксессуары
7.4.3.- ТРЕНИНГ ПО МОНТАЖУ И НАЛАДКЕ
MDU-MLB
The Mobile Structure for MDU, "MDU-MLB", is a robust structure designed to quickly and easily assemble the various elements of the MDU Base Unit, "MDU-UB" or the Computer Controlled Machine Diagnosis Unit, "MDUC", and thus assemble a mobile test...
7.4.3.- ТРЕНИНГ ПО МОНТАЖУ И НАЛАДКЕ
MDU-SM
Настольная структура для оборудования МДУ
A bench-top structure consisting of a slotted table with anodized aluminum frames of 1100 x 770 x 820 mm.It has a transparent protective cover that protects against the rotating parts and allows us to observe the different experiments. The cover...
7.4.3.- ТРЕНИНГ ПО МОНТАЖУ И НАЛАДКЕ
MDU-SSC
Программное обеспечение, датчики и управление для оборудования МДУ
The aim of the vibration analyzer is to assess the machine diagnosis testing with the different kits related to the vibration interface technology.The system consists of two acceleration sensors, a speed sensor, a measuring amplifier with...
7.4.3.- ТРЕНИНГ ПО МОНТАЖУ И НАЛАДКЕ
MDU-BLU
Оборудование для торможения и нагрузки
The Break and Load Unit, "MDU-BLU", of EDIBON is a magnetic particle brake, a display unit and an electrical control. It is possible to precisely adjust the braking moment. The excitation current is used as a measurement of the braking moment and...
7.4.3.- ТРЕНИНГ ПО МОНТАЖУ И НАЛАДКЕ
MDU-SES
Набор упругого дерева
The Set of Elastic Shaft, "MDU-SES", of EDIBON allows to study the behavior of an elastic rotor subjected to imbalance and balance of elastic rotors in operation. It is possible to study the resonance and the phenomena occurred in subcritical and...
7.4.3.- ТРЕНИНГ ПО МОНТАЖУ И НАЛАДКЕ
MDU-SRS
Набор деревьев с трещиной
It is important that fissures resulting from material fatigue in rotating machines are detected in good time before the breakage occurs, which usually leads to fatal consequences.The Set of Rotating Shaft with Crank, "MDU-SRS", consists of two...
7.4.3.- ТРЕНИНГ ПО МОНТАЖУ И НАЛАДКЕ
MDU-SRBF
Набор дефектов подшипников
To determine the remaining life cycle of a roller bearing and decide on its replacement, the slow variation of the vibration spectrum is analyzed. The spectral distribution will enable to draw accurate conclusions about the type of defect and its...
7.4.3.- ТРЕНИНГ ПО МОНТАЖУ И НАЛАДКЕ
MDU-SCO
Набор соединений
The Set of Couplings, "MDU-SCO", allows to compare the properties of different couplings such as curved tooth, bolt, flange and claw couplings.The vibrational behavior of the different types of couplings is important to draw conclusions about...
7.4.3.- ТРЕНИНГ ПО МОНТАЖУ И НАЛАДКЕ
MDU-SBD
Набор для передачи по ремню
The belt drives are noiseless drive devices, have a long life and require little maintenance provided that its design, assembly and adjustment are correct.The Set of Belt Drive, "MDU-SBD", allows to study the conditions that cause vibrations or...
7.4.3.- ТРЕНИНГ ПО МОНТАЖУ И НАЛАДКЕ
MDU-SSDG
Набор дефектов в шестернях
The Set to Study Damage in Gears, "MDU-SSDG", allows to study the vibrational behavior of gears with typical defects.For that purpose, gears with tooth defects and gears without defects are included, so a comparative study can be carried out. The...
7.4.3.- ТРЕНИНГ ПО МОНТАЖУ И НАЛАДКЕ
MDU-SCM
Набор для механизма шатун-кривошип
The compressors and pumps frequently use crank and connecting rod mechanisms. The force and mass oscillations cause vibrations in the units.The Set of Crank Mechanism, "MDU-SCM", allows to adjust the stroke, mass compensation and bearing...
7.4.3.- ТРЕНИНГ ПО МОНТАЖУ И НАЛАДКЕ
MDU-SSCP
Набор кавитации в насосах
Pump cavitation is produced when steam cavities are created within a fluid in which forces act responding to the pressure differences.Cavitation causes noise, damage to components and loss of performance.The Set to Study Cavitation in Pumps,...
7.4.3.- ТРЕНИНГ ПО МОНТАЖУ И НАЛАДКЕ
MDU-SSVF
Набор вибраций в магистралях MDU
In the Blower Vibration Set for MDU, "MDU-SSVF", the vibrations are magnetically induced. It is possible to study three impellers with a different number of movable vanes. It is also possible to study the gyroscopic effect by mounting the flywheel...
7.4.3.- ТРЕНИНГ ПО МОНТАЖУ И НАЛАДКЕ
MDU-SEV
Набор электромеханических вибраций
Among the drive systems are the asynchronous motors, which generate vibrations in machines.This is the case with an asymmetric air gap (space between rotor and stator), in which the magnetic vibrational forces induce torsional and bending...
7.4.3.- ТРЕНИНГ ПО МОНТАЖУ И НАЛАДКЕ
MDU-SD
Датчики перемещения для оборудования МДУ
Two displacement sensors which, together with the Set of Elastic Shaft ,"MDU-SES", and the Software, Sensors and Control for MDU Unit, "MDU-SSC", allow you to represent subcritical and supercritical shaft orbits in resonance.
УПРАЖНЕНИЯ И ПРИМЕРЫ С ИНСТРУКЦИЯМИ
РУКОВОДСТВО ПО ПРАКТИЧЕСКИМ УПРАЖНЕНИЯМ ВКЛЮЧЕНО В РУКОВОДСТВО ПОЛЬЗОВАТЕЛЯ
Practical possibilities with the recommended additional elements (Not included):
Set of Elastic Shaft (MDU-SES):
- Learning about the effects of the balanced and unbalanced elastic rotor.
Set of Rotating Shaft with Crank (MDU-SRS):
- Study of the variation of a typical vibration behavior (vibration velocity, frequency, amplitude, and phase) due to a fissure.
- Identifying cracks and fissures in shafts through acceleration curves and order analysis.
- Identifying a fissure through the variation of a vibration spectrum.
Set of Roller Bearings with Faults (MDU-SRBF):
- Estimating the life cycle of a roller bearing.
- Identifying faulty roller bearings.
- Checking the effects of roller bearing faults on outer and inner ring, or the roller bearing body on the vibration spectrum.
Set of Couplings (MDU-SCO):
- Understanding the effect of ring gear hardness on claw couplings.
- Comparing the curved tooth, bolt, flange or claw couplings.
Set of Belt Drive (MDU-SBD):
- Understanding the importance of belt tension in vibration behavior.
- Checking the effect of the eccentricity in pulleys and the speed in vibration behavior.
- Comparison between defective and non-defective belts.
- Understanding and interpreting the frequency spectra in order to differentiate between defective and non-defective belts.
Set to Study Damage in Gears (MDU-SSDG).
- Identifying defects in the gears according to their vibration behavior.
- Learning about the effect of the toothed gear, the lubrication used and the wheelbase and the backlash.
Set of Crank Mechanism (MDU-SCM):
- Identifying wear on the rod and piston.
- Learning about the effect of bearing clearance and impacts.
Set to Study Cavitation in Pumps (MDU-SSCP):
- Study of the vibrations of a centrifugal pump in operation.
- Understanding the cavitation phenomenon in a centrifugal pump.
- Identifying vibrations caused by the movable vanes in the vibration spectrum.
- Measuring the pitch frequency between movable vanes.
- Measuring the blower vibrations.
Set of Electromechanical Vibrations (MDU-SEV):
- Learning about the effect of an asymmetric air gap on the vibration behavior and the electromagnetic and performance losses.
- Learning about the effect of the electrical windings on vibration behavior.
БОЛЬШЕ ПРАКТИЧЕСКИХ УПРАЖНЕНИЙ ДЛЯ РАБОТЫ С УСТРОЙСТВОМ
Practical possibilities with the recommended additional elements (Not included):
Set of Elastic Shaft (MDU-SES):
- Learning about the effects of the balanced and unbalanced elastic rotor.
Set of Rotating Shaft with Crank (MDU-SRS):
- Study of the variation of a typical vibration behavior (vibration velocity, frequency, amplitude, and phase) due to a fissure.
- Identifying cracks and fissures in shafts through acceleration curves and order analysis.
- Identifying a fissure through the variation of a vibration spectrum.
Set of Roller Bearings with Faults (MDU-SRBF):
- Estimating the life cycle of a roller bearing.
- Identifying faulty roller bearings.
- Checking the effects of roller bearing faults on outer and inner ring, or the roller bearing body on the vibration spectrum.
Set of Couplings (MDU-SCO):
- Understanding the effect of ring gear hardness on claw couplings.
- Comparing the curved tooth, bolt, flange or claw couplings.
Set of Belt Drive (MDU-SBD):
- Understanding the importance of belt tension in vibration behavior.
- Checking the effect of the eccentricity in pulleys and the speed in vibration behavior.
- Comparison between defective and non-defective belts.
- Understanding and interpreting the frequency spectra in order to differentiate between defective and non-defective belts.
Set to Study Damage in Gears (MDU-SSDG).
- Identifying defects in the gears according to their vibration behavior.
- Learning about the effect of the toothed gear, the lubrication used and the wheelbase and the backlash.
Set of Crank Mechanism (MDU-SCM):
- Identifying wear on the rod and piston.
- Learning about the effect of bearing clearance and impacts.
Set to Study Cavitation in Pumps (MDU-SSCP):
- Study of the vibrations of a centrifugal pump in operation.
- Understanding the cavitation phenomenon in a centrifugal pump.
- Identifying vibrations caused by the movable vanes in the vibration spectrum.
- Measuring the pitch frequency between movable vanes.
- Measuring the blower vibrations.
Set of Electromechanical Vibrations (MDU-SEV):
- Learning about the effect of an asymmetric air gap on the vibration behavior and the electromagnetic and performance losses.
- Learning about the effect of the electrical windings on vibration behavior.
АНАЛОГИ ОБОРУДОВАНИЯ В НАЛИЧИИ
7.4.3.- ТРЕНИНГ ПО МОНТАЖУ И НАЛАДКЕ
MDUC
Оборудование для диагностики машин, управляемое с компьютера (ПК)
The Computer Controlled Machine Diagnosis Unit, "MDUC", of EDIBON, allows you to perform vibration measurement practical exercises, measuring the displacement, velocity and acceleration of vibrations in the time-frequency range.The Computer...
ДОПОЛНИТЕЛЬНОЕ ОБОРУДОВАНИЕ
7.4.3.- ТРЕНИНГ ПО МОНТАЖУ И НАЛАДКЕ
ADSG
Оборудование для выравнивания приводов, валов и шестерен
The Drive, Shaft, and Gear Alignment Unit, "ADSG", allows for studying the coupling and uncoupling, maintenance, repair of the related units and checking the operation with the following units:CGA. Combined Gear Assembly Unit.SGA. Spur Gear...
7.4.3.- ТРЕНИНГ ПО МОНТАЖУ И НАЛАДКЕ
MDUC
Оборудование для диагностики машин, управляемое с компьютера (ПК)
The Computer Controlled Machine Diagnosis Unit, "MDUC", of EDIBON, allows you to perform vibration measurement practical exercises, measuring the displacement, velocity and acceleration of vibrations in the time-frequency range.The Computer...
7.4.3.- ТРЕНИНГ ПО МОНТАЖУ И НАЛАДКЕ
MDU-MLB
Мобильная структура для оборудования МДУ
The Mobile Structure for MDU, "MDU-MLB", is a robust structure designed to quickly and easily assemble the various elements of the MDU Base Unit, "MDU-UB" or the Computer Controlled Machine Diagnosis Unit, "MDUC", and thus assemble a mobile test...
7.4.3.- ТРЕНИНГ ПО МОНТАЖУ И НАЛАДКЕ
MDU-SM
Настольная структура для оборудования МДУ
A bench-top structure consisting of a slotted table with anodized aluminum frames of 1100 x 770 x 820 mm.It has a transparent protective cover that protects against the rotating parts and allows us to observe the different experiments. The cover...
7.4.3.- ТРЕНИНГ ПО МОНТАЖУ И НАЛАДКЕ
MDU-SSC
Программное обеспечение, датчики и управление для оборудования МДУ
The aim of the vibration analyzer is to assess the machine diagnosis testing with the different kits related to the vibration interface technology.The system consists of two acceleration sensors, a speed sensor, a measuring amplifier with...
7.4.3.- ТРЕНИНГ ПО МОНТАЖУ И НАЛАДКЕ
MDU-BLU
Оборудование для торможения и нагрузки
The Break and Load Unit, "MDU-BLU", of EDIBON is a magnetic particle brake, a display unit and an electrical control. It is possible to precisely adjust the braking moment. The excitation current is used as a measurement of the braking moment and...
7.4.3.- ТРЕНИНГ ПО МОНТАЖУ И НАЛАДКЕ
MDU-SES
Набор упругого дерева
The Set of Elastic Shaft, "MDU-SES", of EDIBON allows to study the behavior of an elastic rotor subjected to imbalance and balance of elastic rotors in operation. It is possible to study the resonance and the phenomena occurred in subcritical and...
7.4.3.- ТРЕНИНГ ПО МОНТАЖУ И НАЛАДКЕ
MDU-SRS
Набор деревьев с трещиной
It is important that fissures resulting from material fatigue in rotating machines are detected in good time before the breakage occurs, which usually leads to fatal consequences.The Set of Rotating Shaft with Crank, "MDU-SRS", consists of two...
7.4.3.- ТРЕНИНГ ПО МОНТАЖУ И НАЛАДКЕ
MDU-SRBF
Набор дефектов подшипников
To determine the remaining life cycle of a roller bearing and decide on its replacement, the slow variation of the vibration spectrum is analyzed. The spectral distribution will enable to draw accurate conclusions about the type of defect and its...
7.4.3.- ТРЕНИНГ ПО МОНТАЖУ И НАЛАДКЕ
MDU-SCO
Набор соединений
The Set of Couplings, "MDU-SCO", allows to compare the properties of different couplings such as curved tooth, bolt, flange and claw couplings.The vibrational behavior of the different types of couplings is important to draw conclusions about...
7.4.3.- ТРЕНИНГ ПО МОНТАЖУ И НАЛАДКЕ
MDU-SBD
Набор для передачи по ремню
The belt drives are noiseless drive devices, have a long life and require little maintenance provided that its design, assembly and adjustment are correct.The Set of Belt Drive, "MDU-SBD", allows to study the conditions that cause vibrations or...
7.4.3.- ТРЕНИНГ ПО МОНТАЖУ И НАЛАДКЕ
MDU-SSDG
Набор дефектов в шестернях
The Set to Study Damage in Gears, "MDU-SSDG", allows to study the vibrational behavior of gears with typical defects.For that purpose, gears with tooth defects and gears without defects are included, so a comparative study can be carried out. The...
КАЧЕСТВО
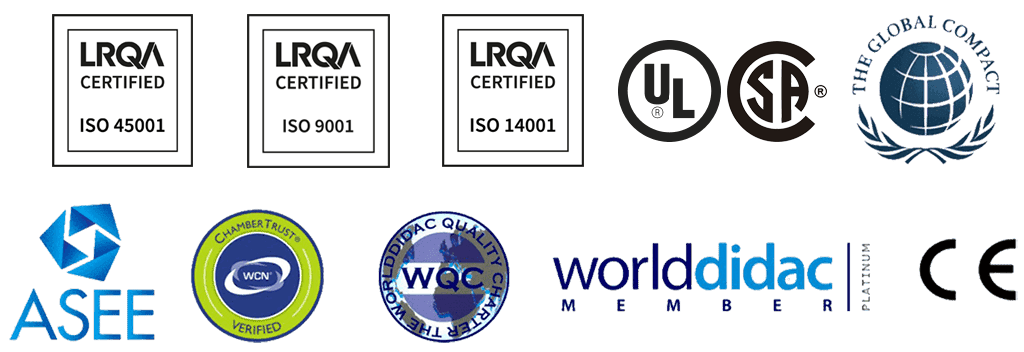
ПОСЛЕПРОДАЖНОЕ ОБСЛУЖИВАНИЕ
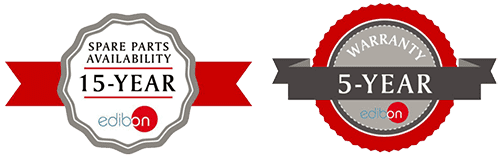